Although straightforward in some ways, PVC can be a surprisingly complex material that extruders make formulaic adjustments to so it can meet a robust and evolving set of performance criteria.
It has to meet handling requirements while it’s being processed, punched, cut, welded, shipped and installed. The installed product needs to perform well in the opening and weather well. “It’s amazing what kind of an engineered piece of product a window and door is,” Greg Koch, vice president of sales and marketing at Deceuninck, says.
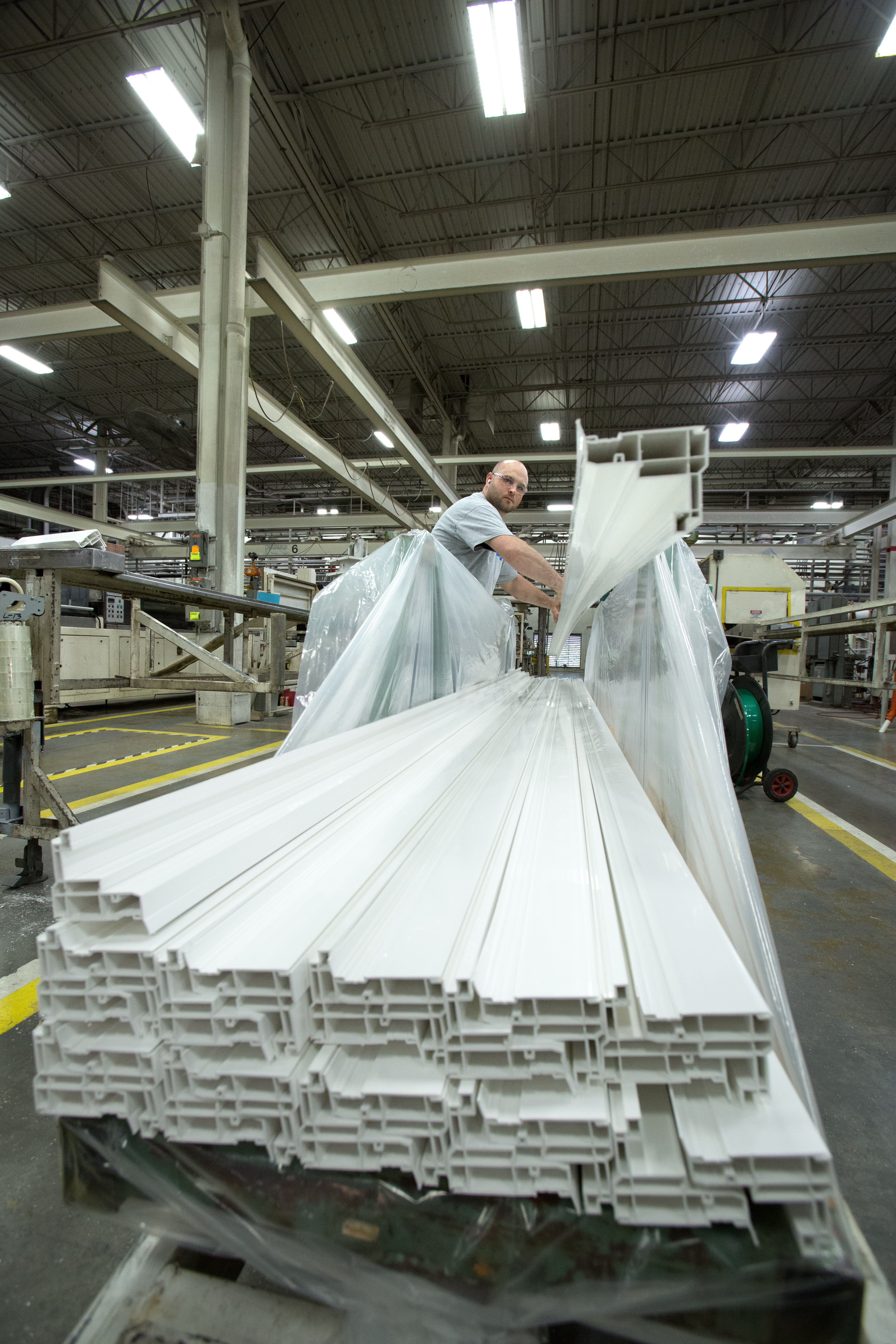
Performance
Extrusions are all tested to minimum AAMA 303 standards, which address weatherability, impact resistance, heat resistance, shrinkage, heat buildup and more. Each time an extruder adjusts a compound in its formulation, it is qualified. “If we’re going to qualify a new impact modifier, heat stabilizer or pigment, we’re only changing one variable at a time,” explains Kevin Seiling, vice president of engineering and new product development, Veka Inc. Then, companies test attributes like bulk density, flowability and torque before optimizing extrusion conditions of the new formulation. Finally, the profile is tested for impact, shrinkage and heat resistance. If it passes all of those test conditions, it then goes into accelerated weathering and out for weatherability testing.
“The professionals in the business very rarely make a mistake with compounding and formulation,” he says. Seiling notes that if there’s a problem in the field, liability can be what he describes as “pretty substantial. … We’re very careful to not put something out in the field we don’t think is better than what we’ve been doing.”
Weatherability: Vinyl had a poor reputation for weathering in the 1980s because the formulations were European-based, and only tested in Europe to a climate that is similar to Toronto, Canada, explains Seiling. As discoloration and field problems related to color change popped up as the vinyl replacement window market expanded, especially South and West, two-year outdoor weathering tests were born.
Eric Thompson, commercial sales manager for Quanex Building Products, explains extrusions are tested in Arizona, Florida and Kentucky to represent hot and arid, humid and sea salt, and hot/cold swing climates, respectively. The geographic diversity of the locations, he says, gives enough testing data to allow the product to be used anywhere in the world and hold up.
The Fenestration & Glazing Industry Alliance currently has two active weathering task groups. One relates to long-term performance, says Seiling. The current program hinges on two years of outdoor weathering. “The requirement is only two years, because after two years the rate of change has slowed dramatically. There’s very little change after two years,” he says. Despite that most vinyl windows in the field are still in service after 20 or 30 years and only come out of service because of remodeling preferences or a desire to upgrade insulating glass, he says, questions loom around how manufacturers can offer longer warranties with only two years of weathering. The task group is exploring what it would look like to extend the weathering for various lengths of time (i.e. three, five, 10 years) and what new performance requirements would be.
Another task group is exploring accelerated weathering and how to correlate outdoor weathering with accelerated weathering such as QUV and Xenon Arc. If proper correlations can be proven, says Seiling, it could fast-track new product development and enable products to get to market faster. That correlation, however, is difficult to determine because color change in vinyl is specific to location, climatic data and start date.
Dimensional Stability: An AAMA 303 study group is discussing if accessory profiles should be added to dimensional stability requirements under AAMA 303. Currently, the frame, sash and other structural components are certified, but glazing beads, trim pieces and accessories are not, explains Seiling. Those components do require weathering performance, and the task group will determine if dimensional stability testing is also necessary and, if so, at what level.
Bending Strength: Some extruders try to improve the bending strength of profiles with fillers such as wood fibers, chopped glass fibers and other minerals, says Seiling. “Although bending strength can be improved, it’s generally inversely proportional to severe reductions in impact resistance, weld strength and weathering.”
Color solutions
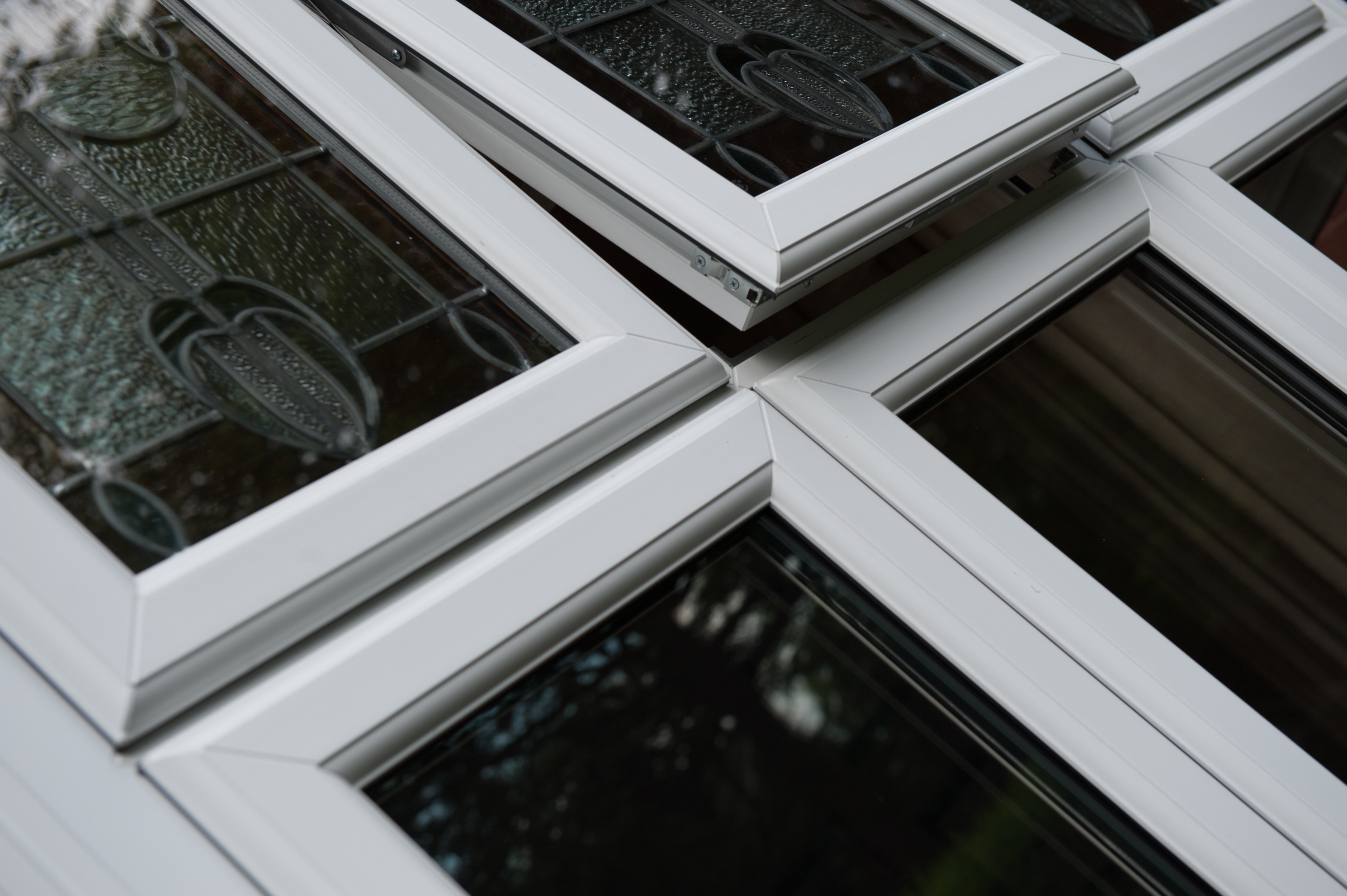
Basic PVC extrusion colors are in pigmented white, almond, beige and clay/putty, says Seiling. “Once the colors get darker than that, there’s not sufficient technology developed in PVC extrusion to handle both heat buildup and weathering. Generally you get one and you sacrifice the other,” he says.
Several solutions exist, says Seiling, such as paint, laminates and capstock. Paint is governed by AAMA specifications for paint on vinyl and heat buildup. Laminates, he says, have low heat buildup and strong durability and weathering attributes because the top layer is acrylic or PVDF. Acrylic capstocks are coextruded and therefore integral to the extrusion.
“You don’t have to sacrifice aesthetics for performance,” says Thompson. Quanex, for example, uses its own technology that is thermally fused to the extrusion without modifying the base extrusion. “It is a color cap that is formulated with pigments and acrylic modifiers that create a durable, harder surface,” says Thompson, going on to say the color is IR invisible so that light can pass through it, thereby negating heat buildup and color and material degradation.
Thompson notes that color technology continues to evolve from a performance and energy standpoint. “When you co-extrude a color, you’re only handling that product once,” he explains, as opposed to other options such as laminate and paint that require the product to be handled multiple times, thereby increasing the overall cost. “Co-extrusion color technology is continuing to grow across the industry.”
When it comes down to it, flexibility is key. “If you can’t have flexibility, you’re really handcuffed,” says Koch. “We need different solutions with different customers in different areas of the country because they’re all facing different challenges.”
One challenge of darker colors is heat buildup. Koch explains the key component in weatherability is titanium dioxide, most of which is found in white paint and is what keeps the extrusion from yellowing. Darker colors, however, make it difficult to include the titanium dioxide, thereby making weatherability of darker colors more challenging.
Those dark colors also absorb heat, which can affect material stability. Deceuninck issues guidelines for its darker profiles, including inserting reinforcement to the vinyl profile, opening the closed chambers of the windows for ventilation and, from the installation perspective, ensuring the window opening allows sufficient space for the product to expand when it gets hot. “It starts with materials, but then there’s also guidance that our application team provides to the customers,” Koch explains. “You have to manufacture it a little bit differently; then when it gets installed, it has to be controlled as well.”
Sustainability
Much focus in the building world lies in embodied carbon, or the amount of carbon required to produce all of the materials that go into a structure such as concrete, steel and glass. “What that tells me is that if I had a choice between building a new building or remodeling one, I should remodel one,” says Seiling. “There’s no embodied carbon; it’s already sitting there.” That means remodeling and repurposing buildings likely will dominate for the next few years until occupancy rates recover.
Deceuninck recycles its manufacturing scrap and is in its ninth year of being Green Circle certified for recycled content, says Koch. “We are also continually assessing our manufacturing processes and energy usage to reduce waste and consumption.”
Deceuninck’s parent company operates a recycling plant in Belgium that recycles end-of-life product to produce several recycled waste streams, but Koch notes this is more difficult in the U.S. with longer distances. “Most U.S. window fabricators already work with a local scrap company to recycle their end cuts,” he says. “It is one of our goals to start to recycle customer scrap into our products. We are investigating how this can be done in a sustainable way.”
Thompson says up to 25 percent of Quanex’s profiles are made from post-industrial waste. The company uses its own scrap to make up the recycled content, he says.
At the end of life, vinyl windows can be disassembled and the various parts—including the glass, EPDM gaskets, vinyl and any steel or aluminum—can be recycled. “Vinyl windows have a huge future in the green space going forward,” Seiling says. “The amount of recycling capability at end of life is much better for vinyl windows than other products for punched openings.”