Going all in on in-house Manufacturing
The fenestration industry is taking control and reshaping automation by adopting in-source manufacturing to boost efficiency, grow customization and enhance resiliency
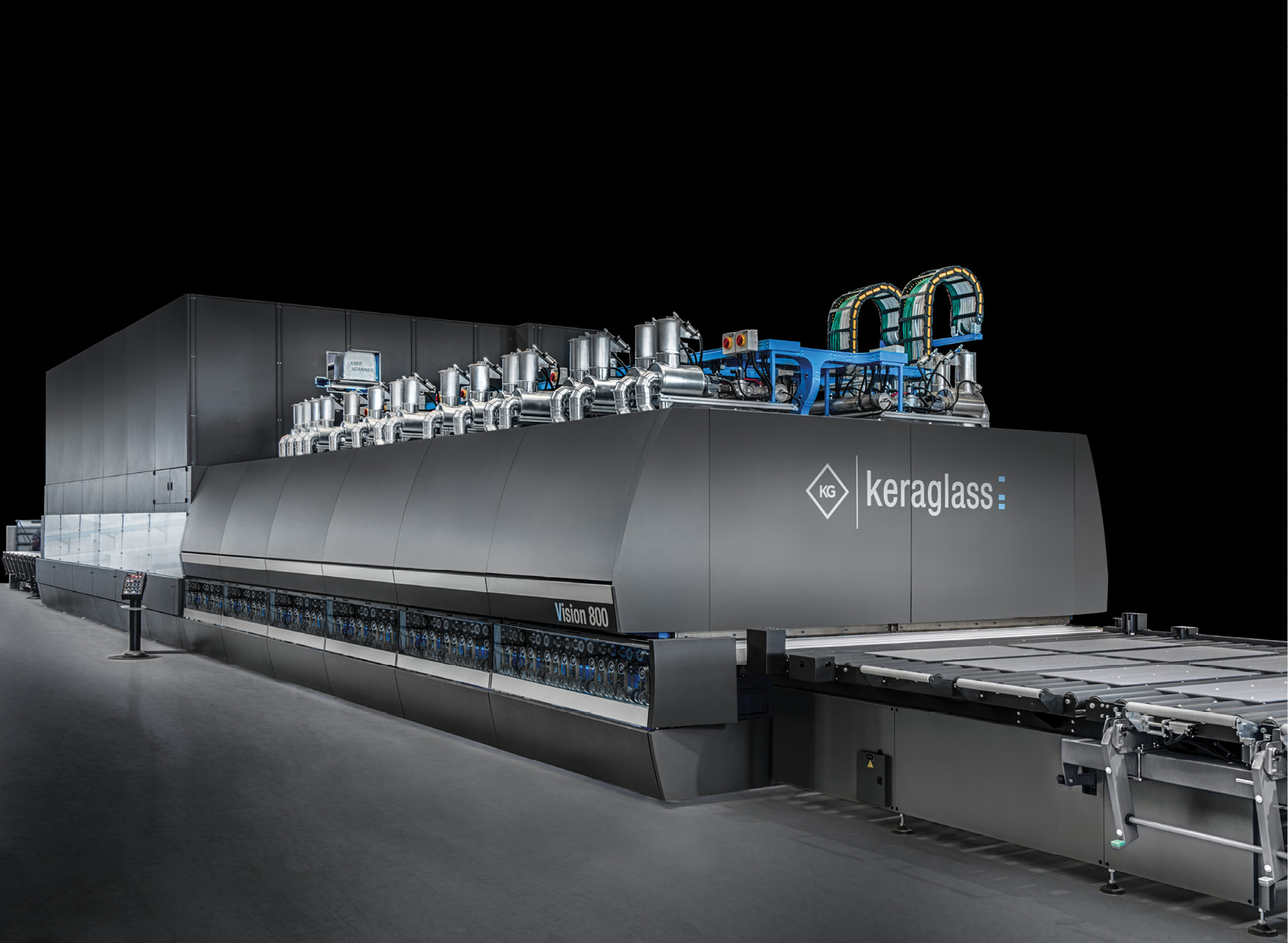
Above: The Vision 800 oscillating tempering furnace offers customizable solutions for architectural glass. Photo: Keraglass SrL
The adoption of automation in the fenestration industry is accelerating as demand for windows and doors remains robust and the labor market remains tight. Companies are increasingly turning to automation to manage diverse product lines. This shift has led to a greater need for efficient material handling, heavy-lifting capabilities and machinery that can accommodate new product innovations. High-speed automation is becoming essential for manufacturers to maintain productivity and meet market demands.
In March, John Burns Research and Consulting reported that 19% of residential window and door companies expected to focus on production automation in the next 12 months. And at the beginning of the year, Window + Door’s 2024 Industry Pulse reported that 41% of residential fenestration companies plan to invest in purchases and upgrades of machinery to free up available labor for more value-added tasks, a 38% difference increase from last year’s survey.
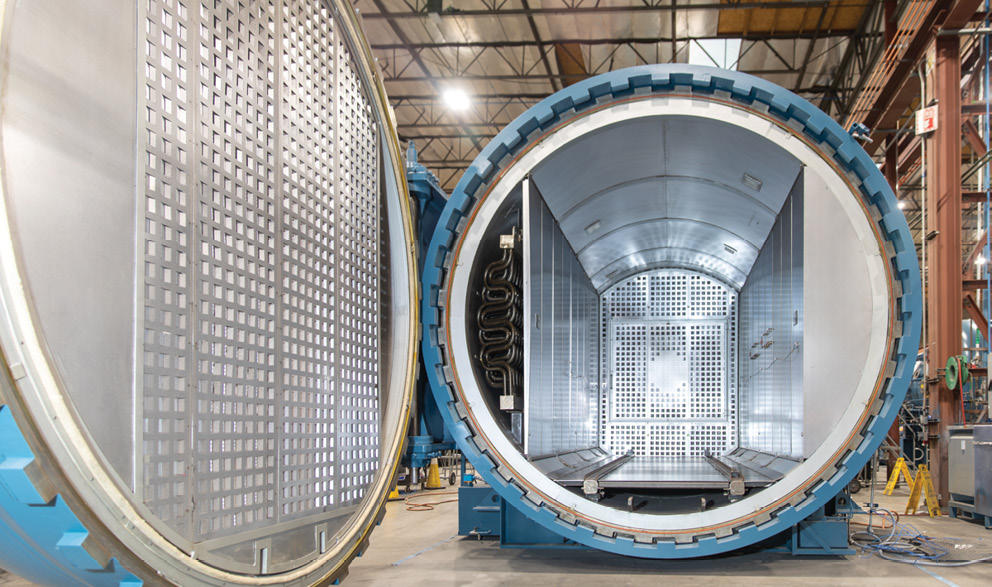
Supporting increased production
An increase in automation can influence the decision to bring manufacturing operations in-house. If the benefits of reduced labor costs, improved efficiency and quality control outweigh the costs of setting up and maintaining in-house manufacturing facilities, companies might find it more economically viable to bring production in-house. In-house manufacturing can also allow for quicker customization and shorter lead times, greater control over product development and customization, reduced reliance on external suppliers and risk of supply chain disruptions, and protection of proprietary information and processes. It can even elevate safety by reducing human touchpoints.
In Window + Door’s 2024 Top Manufacturers Survey, three-quarters of respondents indicated they already fabricate insulating glass units in-house, and almost two-thirds have other in-house operations, including extruding, laminating, tempering and more. Most already use automation in their business and two-thirds plan to add more in the next year.
In particular, the insulating glass production market is projected to double in both size and value within the next six years, according to Business Research Company, with the largest surge coming from growth in residential construction. And as the need for more multi-unit properties grows, residential construction will continue to drive demand for insulating glass windows.
“Triple-glazed windows will continue to be a discussion point and focus for future growth,” predicts Morgan Donohue, president, Erdman Automation Corp., in the 2024 Industry Pulse. “[There will be] constant improvement for product performance on the window side.”
Machinery and automation
57%
Added production capacity
in 2023
71%
Plan to add capacity in 2024
16%
Use AI in the business
Source: 2024 Industry Pulse
Strategic in-house automation
In speaking to the benefits and drawbacks from doing more in-house rather than outsourcing, Laura Phillips, vice president of engineering, Pella Corp., says numerous options must be considered. “Our vertical integration strategies are considered capability by capability. Each time we decide to make instead of buy, we consider the impacts across the value chain,” says Phillips.
“At Pella, this decision is about more than just cost. We answer questions like whether the capability aligns with our organizational strategy; whether in-sourcing reduces organizational risk; whether we can produce it efficiently, safely and with high quality; whether we have an accessible workforce; and whether it will contribute to our profitability. Each decision must be weighed carefully, as there are pros and cons with every make-or-buy scenario.”
The current state of the industry, characterized by supply chain disruptions and labor shortages, is compelling organizations to adopt a more in-house manufacturing approach, says Bruce Wesner, senior director of automation and reliability, MITER Brands. “Recent supply chain issues and availability of skilled and production labor shortages are driving organizations to vertically integrate (in-source) more into their manufacturing strategies to be able to ‘control the controllable’ more effectively,” says Wesner. “Building a capable internal team to support new processes and advanced technology is critical. Adding automation to offset operations labor challenges that drive safety, quality and productivity needs to be central to in-sourcing. Developing an internal support team along with partner OEMs that work closely to ensure optimum productivity is essential.”
A large segment of the market is already heavily invested in automating insulating glass unit manufacturing to meet the growing market demand. “Alpen is making the most significant equipment investments in its history to automate and significantly scale thin-glass triple- and quad-pane insulating unit glass manufacturing capacity,” says Tim Maierhofer, chief operating officer, Alpen High Performance Products. “Our motivations for investing in this automation are centered on a desire to ‘meet the market moment’ by allowing the company to feed thin-glass IGUs to window and door manufacturers interested in this solution for their own product lines. Window and door manufacturers need short lead times and reliable suppliers producing high-quality products that can keep up as their demand grows.”
Labor
21%
Report more difficulty finding workers in 2023, compared to 50% in 2022
91%
Plan to hire new workers in 2024
34%
Recruitment is biggest labor challenge
Source: 2024 Industry Pulse
In-house learning curves
A significant labor shortage has the fenestration industry looking to attract and retain younger talent. Companies must prioritize ergonomics, automate repetitive tasks so employees are free to perform more value-added functions, and offer engaging, technology-based work environments. In-house work offers engaging opportunities for those businesses willing to address learning curves, offer additional training or enact strategies to manage the transition.
“In-sourcing processes and adding automation always come with challenges. Simple things like assuring adequate initial and ongoing training are planned and executed, along with making sure appropriate critical spare parts are available to drive equipment uptime and availability,” says MITER’s Wesner. “The use of new technologies like augmented reality service support is relatively new and can be critical to provide visual assistance to technical support teams that may not be able to be directly hands-on with equipment downtime events. The AR technology can also be used to teach maintenance and automation team members who may not have all the skills or competency needed to do the work.”
For Pella, automation has been an effective tool to improve the experiences of both customers and team members. “It has helped Pella become more reliable for our customers and has made difficult manufacturing jobs easier, resulting in improved team member engagement and retention. With more automation in our plants, our team has focused on elevating technology acumen through training to extract value from the automation and to sustain and improve it over time,” says Pella’s Phillips. “We have also built teams with deep technology expertise to develop and deploy automation across our operations. In many cases, these capabilities allow us to be more proactive in our decisions about what we can insource.”
“Because of the increase in equipment complexity created by automation, Alpen has added management leadership and engineering skills experienced in automation and controls programming,” adds Maierhofer. “Alpen has also committed to partnering with local educational institutions offering technical degrees by setting up robust internship programs with students to develop skills in areas like CNC programming and controls.”
Quantifying investment and ROI
Companies invest substantial capital into automated machinery and, as such, return on investment is an important calculation. Many expect to see it within 24 months. The decision to bring manufacturing in-house can be influenced by initial investment costs, technological advancements, industry trends and global economic conditions, which can vary by company and individual circumstances.
Automation and retirement of old equipment are the two main growth areas in 2024, according to Mike Biffl, vice president of sales and marketing, Sturtz Machinery, who spoke in the 2024 Industry Pulse about the upcoming need for machinery manufacturers to modernize their manufacturing plants. “We do not see as much capital investment for companies trying to increase production as much as see them moving to update machinery that is nearing its end of life,” says Biffl.
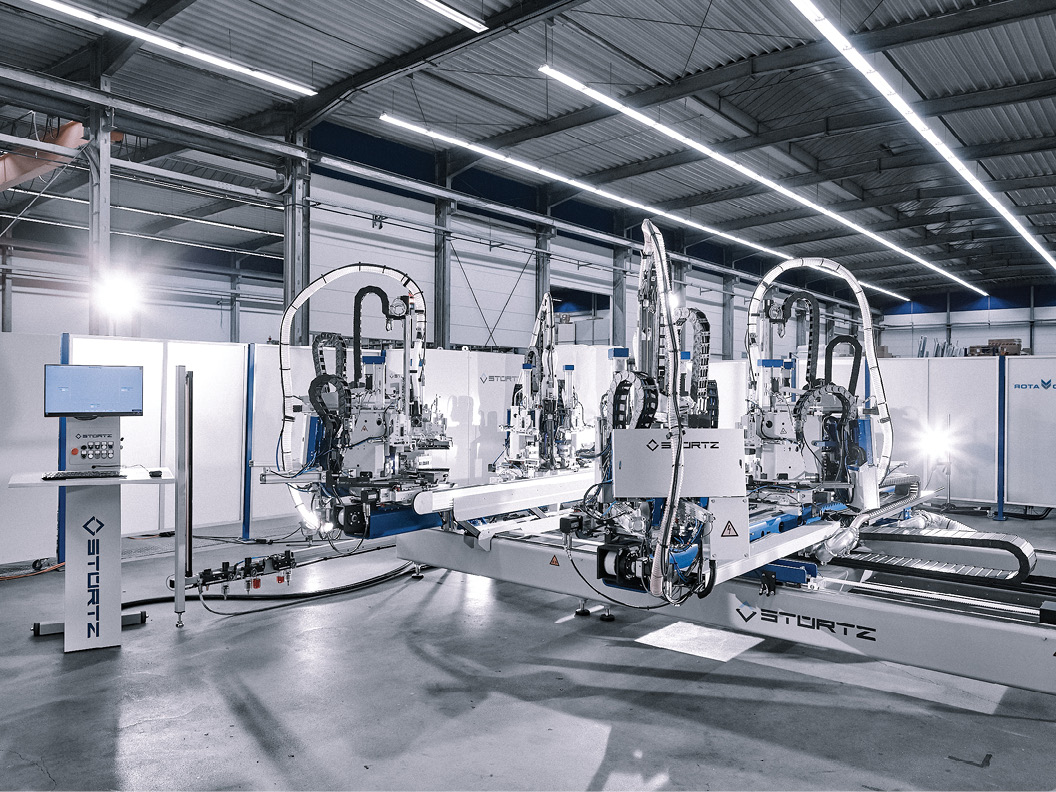
“Achieving ROI is always the goal,” says Wesner. “We have seen improvements in safety by eliminating the human factors of lifting heavy materials, repetitive trauma, etc. And we have seen significant savings on the quality side, too, by having the new technology and automation improve processes, yielding improved first-pass quality and significant improvements in field warranty defects.”
“To the extent of making the case for investments, Alpen has done extensive work to model expected returns on investment for equipment being added to the company, but validating those models isn’t yet applicable to Alpen as our investments are largely coming at us now, or will in the near future,” says Alpen Chairman Brad Begin. “Based on our experience to date, however, we are confident our conservative assumptions are likely to exceed expectations—particularly on the demand side of the equation.”
Pella sees automation adding value across many operational categories including safety, quality, delivery, profitability and team member engagement. “A few key principals we use to guide decision-making on automation include not automating bad processes and making sure the opportunity or problem to solve is clear,” says Phillips. “We believe that robust operational processes and culture enabled through technology unlock maximum value.”
Investing in in-house manufacturing remains a solid strategy for any manufacturer looking to optimize their outputs with the right equipment and processes.
Signs it’s time to bring it in-house
For companies looking to help boost manufacturing and take control of their processes, in-house manufacturing offers a way out of the outsourcing cycle. But determining when to make the switch to in-house is challenging. Here are five signs it might be time to bring it in-house:
- You need improved quality control. Outsourcing requires due diligence on whether the end product you receive meets your standards. In-house manufacturing offers full control over the production process, easily allows for product or process changes, and provides more flexibility across the production pipeline for as-needed updates and adjustments.
- You need better flexibility. Manufacturing in-house gives you a lot of flexibility to easily change or alter the product as it’s being produced. If you discover an outsourced product needs a last-minute change, it takes time to contact the manufacturing company and implement it.
- You need shorter lead times. Customers that receive their products faster lead to loyal customers and less concern over meeting deadlines due to shipping delays. Improved loyalty leads to higher order volume. You can produce and deliver more quickly, creating a loop of long-term ROI to alleviate the initial costs of moving manufacturing in-house.
- You need better cross-team communication. With manufacturing coming in-house, there is total access to the entire manufacturing team and increased visibility into the production process, allowing for efficient communication, improved research and development, and better products.
- You need IP protection. In-house manufacturing helps ensure that a company's intellectual and physical property remains theirs.
Expanding production footprints
Nearly half of companies this year indicated they will expand production capacity, according to the Industry Pulse Report. Some have already done so in the past two years—and plan to continue doing so—by expanding their facilities.
- YKK AP America broke ground late last year on a residential window and door manufacturing facility in Georgia, which will include modern equipment and increased production capabilities.
- Veka has spent more than $50 million in the past two years to boost capacity at its North American sites, adding lamination lines at two of its locations.
- Last year, Marvin Windows & Doors announced plans to make huge investments in automation and technology upgrades, central to a five-year business strategy.
- Viwinco Windows + Doors debuted a 70,000-square-foot glass facility in Pennsylvania, with automation covering a variety of processes, including cutting, seaming, tempering, laminating and insulated glass fabrication. Its next project will overhaul the vinyl facility, investing in new automated equipment and technology.
- Quaker Windows & Doors to broke ground on a new Eldon phase III expansion, centering around a new powder paint line that will increase capacity.