Process Improvements
How high-speed welding and cleaning increases production capacity in an existing footprint
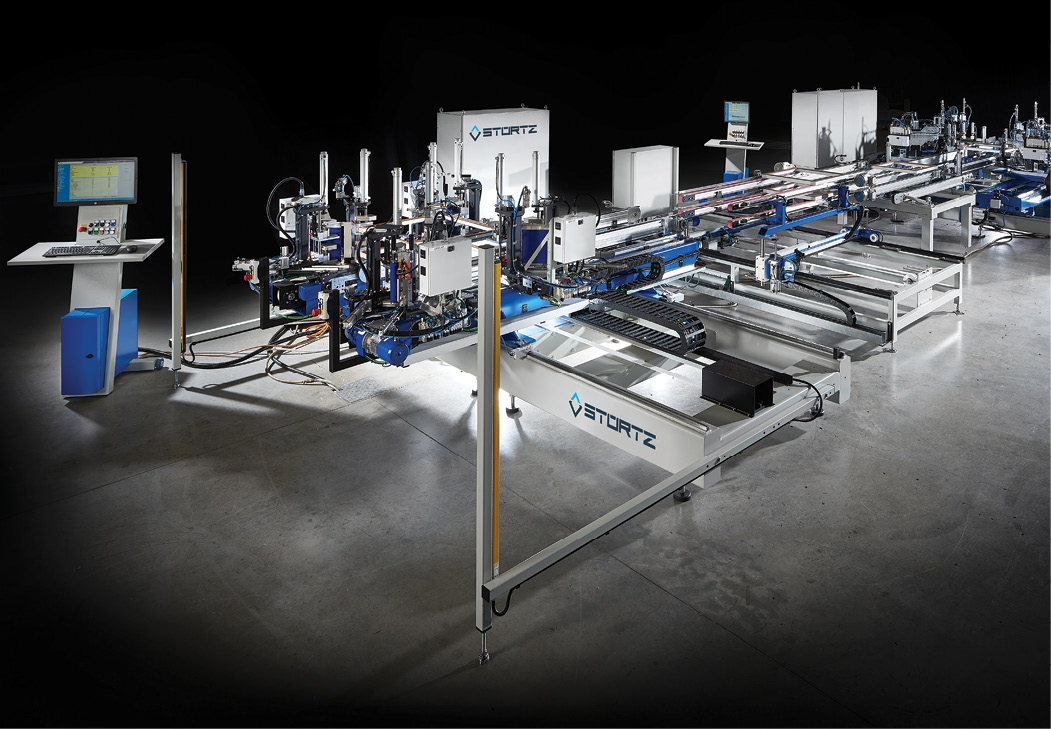
The best current technology in welding and cleaning is more evolutionary than revolutionary. Our industry has its challenges and some of the time-proven concepts remain the most reliable and efficient methods of production. Incremental improvements allow window and door fabricators to continue growing without major plant overhauls or building expansions.
It wasn’t always smooth, but our industry is one of the fortunate sectors of the economy that weathered the past year’s challenges and actually got stronger. Despite COVID-19, material shortages, business disruptions and a major shift in how we collaborate, window and door manufacturers continue to grow during this time.
To keep up with that growth, the demand for capital equipment and improved methods of manufacturing has never been greater. Much of that demand is to allow increased production capacity in an existing footprint. Over the past several years, many machinery manufacturers have invested in R&D efforts to provide exactly that.
High-performance turbo welding and high-speed corner cleaning are becoming the norm in PVC window fabrication. Significant resources have been dedicated to improving the process and getting increased production from a machine with the same footprint while maintaining a consistent flow through the line.
Welders
Current state-of-the-art welders take advantage of servo technology to increase speed, reduce maintenance and provide a more consistent product than previous generations of welders. The main area that benefits from this technology is the melt and push motions. Traditionally achieved with air cylinders, this has long been a limiting factor in speed and consistency. As air pressure fluctuates throughout the plant, melting and joining pressure can vary from one cycle to the next, creating inconsistent weld strength and alignment.
Servo driven motions are shorter, faster and provide consistent operation on every cycle. The added control also has the capability to provide increased pressure and to vary that pressure consistently as the material melts and as it cools. Combined with higher temperatures, this technology reduces machine time by up to 30 percent per weld cycle. Loading and unloading times remain unchanged, but the significant reduction in machine time creates a far more efficient machine in the same overall footprint.
Corner cleaners
If your corner cleaning won’t keep up with faster welding, however, then all you’ve done is create a new bottleneck. To maintain a consistent line flow, increase production and remain in the same footprint, corner cleaning technology has also been a focus of improvements in recent years.
Again, the intelligent use of servo controls has allowed for added speed while maintaining a consistent footprint. By splitting a single servo axis into two—generally a top and a bottom—the machine can now run multiple tools concurrently, the distance each tool needs to travel to and from a home position is reduced and machine speed increases similarly to the 30 percent we see on a turbo welder. This provides a consistent flow of product down the line, eliminating a potential bottleneck at the cleaner.
Information transfer
Automating the transfer of information to the cleaner has also proven beneficial in the welding and cleaning area. The old way of hanging sensors on the machine to try to measure the profile, or independent measuring devices mounted in the cleaner, are unreliable and limited in what they can tell the cleaner.
The more information you can provide to the corner cleaner, the faster the machine can pull up the required program and, in the case of a two- or four-head cleaner, the more quickly it will move to size. Waiting for a measurement system or the operator to manually open the heads to a close size and then fine-adjusting once the part is in the cleaner slows operations.
Barcode scanning direct networking of the welder to the cleaner are the methods of choice in today’s manufacturing environment to combat these shortcomings. Barcode scanning is ideal in a scenario where multiple welders may feed one corner cleaner because it allows a welded square to be brought from anywhere in the plant. By scanning the barcode, the cleaner knows exactly what size and what program it needs to run. In the case of an automated line where one welder always feeds the same cleaner, a network connection is the quickest and most reliable way to pass information to the cleaner.
In short, the best current technology in welding and cleaning is more evolutionary than revolutionary. Our industry has its challenges and some of the time-proven concepts remain the most reliable and efficient methods of production. Incremental improvements allow window and door fabricators to continue growing without major plant overhauls or building expansions.