Product Testing: Where the Lab Meets Real Life
Real-world testing for real-world reliability
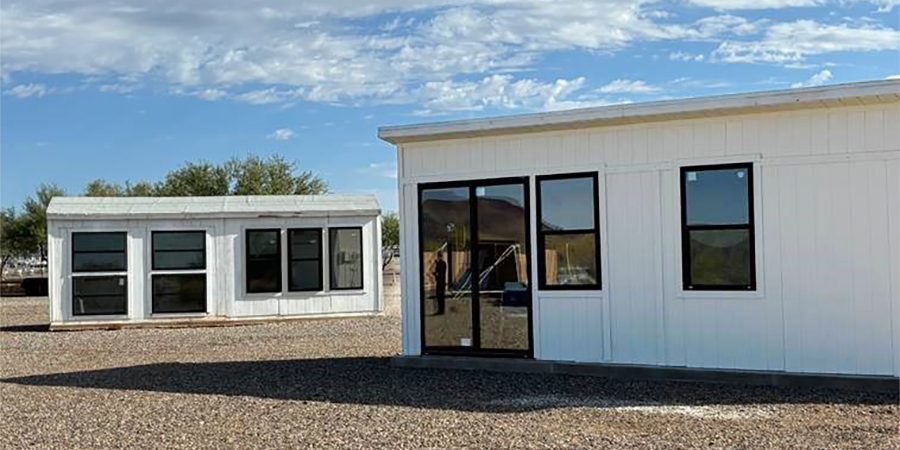
Above: Deceuninck North America's testing huts north of Phoenix, Arizona, resemble real homes.
In today’s modern construction environment, specifiers face a diverse and challenging checklist when selecting building materials that meet the demands of performance and aesthetics.
From ensuring safety and compliance with evolving building codes to verifying performance and enduring visual appeal, each consideration plays a crucial role. And as expectations rise, so does the need to assess how each product will influence the thermal performance and structural integrity of the building.
At the same time, the fast-paced construction industry places pressure on manufacturers to accelerate time to market for new products, helping them secure a competitive advantage in the market.
Consider the downside: Nearly 30,000 new products are introduced across industries each year, and 95% of them fail, according to an article published by Forbes. While new products often require weeks, months or even years of researching and planning, those initiatives are only one part of the overall equation for product development and commercialization. Once a prototype is in place, real-world product testing becomes essential, allowing manufacturers to gather critical insights on how the product will perform in a real-life scenario.
It is not just about meeting the regulations, either. It means delivering products that specifiers, builders, owners and occupants can trust. Through rigorous product testing, companies can identify and address potential defects or challenges before the product reaches the consumer, ensuring safety and satisfaction.
When it comes to window systems for both residential and commercial construction, real-world testing ensures compliance with the most stringent energy codes and sets the standard for performance, safety and reliability.
Field testing versus lab testing
Product testing for windows and doors generally falls into two main categories: lab testing (to AAMA standards) and real-world exposure testing. Lab testing focuses on evaluating performance metrics such as air and water leakage, impact resistance, structural integrity and other critical attributes. These tests are conducted in a highly controlled environment that regulates factors like light, temperature, humidity and other variables. These processes ensure consistent conditions but may not fully replicate the uncertainty of outdoor environments.
This is where real-world testing comes in.
Using this method of testing exposes the window and door systems to outdoor environments, including extreme heat, cold, UV exposure and other weather-related factors.
This is why Deceuninck North America utilizes both testing methods for many of its window and door systems. The organization conducts AAMA testing on-site in its testing lab. In addition, compound samples are sent to a third party for cell class testing, which assesses and categorizes a PVC material’s properties such as impact resistance, tensile strength, stiffness, density and heat tolerance. These tests are conducted to ensure a material’s durability and performance in a range of potential environments.
After this initial testing, the extrusions undergo additional UV and weatherometer testing in a dry chamber for an extended period; many materials are tested for more than 10,000 hours in accelerated testing chambers. This simulates the effects of sunlight and heat to evaluate the extrusion’s durability and long-term performance. Deceuninck extrusions also go through wet and dry cycles in a Q-Lab Ultraviolet machine for additional accelerated weather testing that simulates the effects of sunlight, rain and dew on materials. Additional in-lab tests evaluate color stability, gloss and other aesthetic qualities, while also comparing extrusions against competitor products.
Finally, in-lab testing includes putting extrusions in temperature chambers that vary between hot and cold swings to measure thermal expansion and contraction. The material compounds are also tested for processibility to ensure that they can be extruded efficiently for consistent production and eventual performance once installed as a final window system. Impact testing is also conducted on the extrusions at high and low temperatures, which includes testing a fully assembled window to determine its capacity to resist projectiles—such as 4-inch by 4-inch lumber—launched at hurricane-force speeds.
The true test: Arizona test huts
Darker color window frames and extrusions are becoming increasingly popular, yet they bring challenges in fade resistance and managing expansion and contraction. Addressing these considerations early in the innovation and manufacturing process is crucial to aesthetic and structural longevity. Darker colors tend to show more dirt, but how does the product hold up in extreme weather conditions such as in Arizona—one of the driest, hottest climates in the U.S.?
To further understand this and as an added layer to lab testing, Deceuninck North America constructed a testing hut that resembles a real home north of Phoenix, Arizona, more than 30 years ago. This structure is equipped with full window assemblies.
Fast forward to the 2020s, and a second hut was constructed to put an all-new product line, Eclipse, to the test. Eclipse is a black solid color PVC extrusion that combines aesthetics and performance developed in response to increasing market demand for dark-colored profiles. The slightly larger hut in Arizona is outfitted with Eclipse windows and patio doors. Much like its sister hut, this hut replicates a real home with air conditioning kept at 72 degrees Fahrenheit, exterior wall insulation and a standard roofing system. It also includes windows with similar dark-colored laminates for comparison purposes.
Eclipse has delivered exceptional performance, standing up to the elements for two summers. Temperatures are measured via thermal couples that Deceuninck installs on the windows, and the window system has endured temperatures as high as 111 degrees. In these temperatures, the material itself reached a surface temperature of up to 145 degrees. In addition to Eclipse, Deceuninck’s bronze profile was installed in a testing hut in early 2020, bearing five summers in a scorching, dry climate while satisfying its expected performance.
By putting the company’s windows through this form of outdoor testing, scientists and researchers at Deceuninck can gather extensive data for a more holistic view of window and door system performance. This approach benefits the organization, customers and the industry as a whole.
The Deceuninck research and development team travels to Arizona to measure any potential color change or degradation in the installed systems. In addition, the team will occasionally remove units for closer examination with special instrumentation. This is needed because changes in the window systems have been negligible to date and have not been visible to the human eye upon initial inspection.
Raising the bar
Backing window and doors systems with comprehensive lab and real-world product testing gives buyers, builders and owners peace of mind. However, it also informs future innovation for manufacturers looking to push the industry forward. Product testing identifies any gaps in performance and allows manufacturers to discover the “why” and look for solutions for better formulations, tooling and manufacturing processes.
With a combination of cutting-edge lab testing and rigorous real-world scenarios for further data gathering and analysis, organizations remain committed to ensuring that products exceed industry standards.