Progress Never Stops for Window Manufacturers
Success in today’s window and door space requires striking the right balance between efficiency, performance and consumer preference
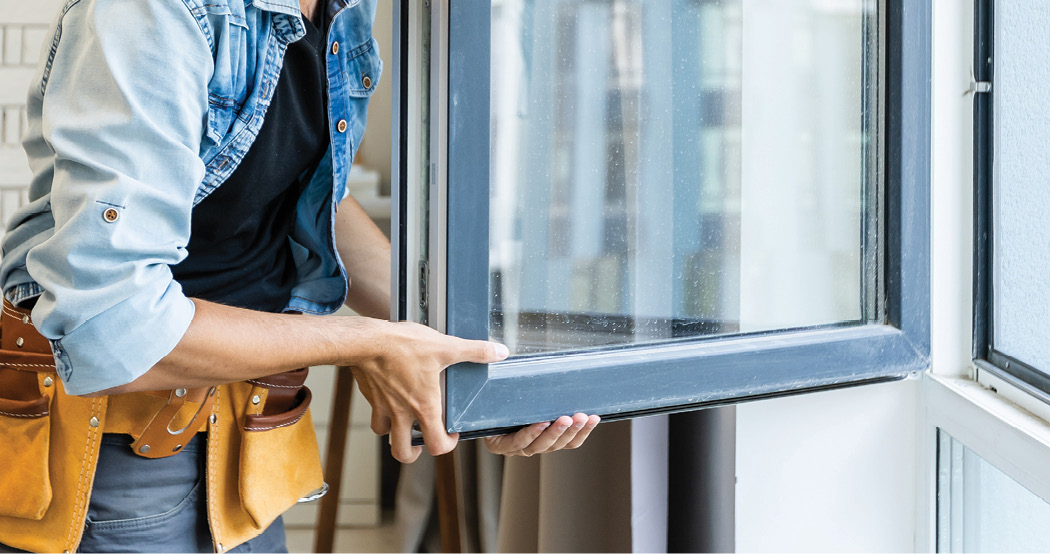
The Bottom Line: Window and door manufacturers must continuously innovate and balance industry trends and new technologies to meet evolving performance standards and succeed in a competitive market.
The slow march of progress never stops when it comes to energy efficiency demands for window and door manufacturers.
Energy Star 7.0, which is approaching its one-year anniversary, is just one example. Government bodies around the world, from the local level to the national stage, are more concerned than ever with fostering greater sustainability in all areas of society. We’ve seen the effects throughout North America, Europe and beyond, as new building codes in major municipalities demand higher levels of performance from all types of buildings.
It’s easy to imagine that several years from now our industry will find itself in a scenario where the Energy Star 7.0 criteria are simply table stakes. Success will involve making investments in forward-thinking technology that can deliver on increasingly lofty expectations.
Of course, that’s not the only thing window and door makers have to worry about. Success in our industry requires striking a careful balance between performance demands and several other criteria. As we head into tradeshow season—a prime opportunity for industry stakeholders to explore new technologies and new ways to do business—here are a few things to consider.
Balancing performance with trending demands
Energy performance isn’t the only moving target that window and door manufacturers need to hit. Consumer preferences are always changing, and they’re continually bringing our industry in new directions.
For example, this magazine noted in its recent survey of the window market that tilt and turn windows—common in Europe—are gaining significant traction in the U.S. market, particularly on the East Coast. Part of this traction is, indeed, due to energy efficiency. All things being equal, tilt and turns’ compression sealing and multipoint locking make them inherently more efficient than, say, double-hung windows.
Window and door makers can and should approach tilt and turn profiles with a careful eye, though. European climates aren’t as demanding as those in North America, and it’s important your windows can stand up to domestic weathering demands. When in doubt, when vetting profiles be sure profile options meet the appropriate AAMA standards for weatherization and performance.
Thin triples’ potential
Evaluating cutting-edge insulating glass technology is essential when working to meet higher energy standards. To those ends, you’ve probably heard about thin or skinny triples.
Thin triples—triple-paned IG units that utilize an ultrathin center lite—
exist in a weird space in the window and door market. In theory, skinny triples represent an effective way to hit new efficiency targets. In 2024, they’re on the table as a way for residential window and door manufacturers to meet recently minted Energy Star 7.0 figures. But despite the performance advantages, they simply haven’t achieved any kind of meaningful market penetration.
Hitting 7.0 numbers today has predominantly involved the use of traditional triple-paned units, or else a complete redesign of a 6.0 system that relied on double-paned. Neither of these options are exactly convenient for manufacturers. Fabricating triples involves significantly more raw materials in the form of an extra pane of glass and additional spacer to seal two argon chambers. Meanwhile, the resulting systems are heavier and deeper, raising some additional considerations when it comes to installation.
And now that the rubber is meeting the road when it comes to delivering Energy Star 7.0, I’ve heard some newer rumblings about thin triples. And there’s good reason for it. Thin triples can drop into the same sash as a conventional double-paned IG unit, enabling manufacturers to utilize their existing systems to meet new requirements. There are some manufacturing processes that need to be ironed out, but that can be done by working with the right partners. For window and door manufacturers, it’s worth staying open-minded.
More than glass
As noted, it’s important to consider your window profiles in meeting higher performance standards. A basic vinyl framing system combined with a high-performing triple IG (or indeed, a thin triple) may get you to the required performance criteria, but it’s possible you may need to incorporate additional elements to hit the new targets. Foam filling could help bridge the gap—but that’s an extra step in your manufacturing process that may add some unnecessary complexity.
Instead, consider choosing a higher-performing vinyl system designed for elevated thermal performance. Off-the-shelf options that come pre-foam-filled, or with cavities small enough to rule out the need for foam at all, may be able to help you achieve the necessary performance targets in a simpler way. Changing your framing system does come with some complexity, and there can be a learning curve to getting a new framing system online and working with it effectively, but it represents an investment in your business’ future that may pay dividends down the road.
Elsewhere, the right profiles can help you stay on trend. High-performance color technologies, like co-extrusion, can better enable you to deliver in-demand black windows and doors without the extra step of painting or laminating. The same profile from the right supplier may offer sound control properties, another attractive feature particularly in busy urban areas.
So, how are you approaching energy efficiency in 2024 and beyond? How are you gauging shifts in customers’ demands? And how are you going to deliver? GlassBuild is right around the corner—and I’m looking forward to discussing all of these things with customers, partners and stakeholders. See you at the show!