Q + A with VEKA | To a Greener Future
How VEKA is making strides to make their company and the industry as a whole more sustainable
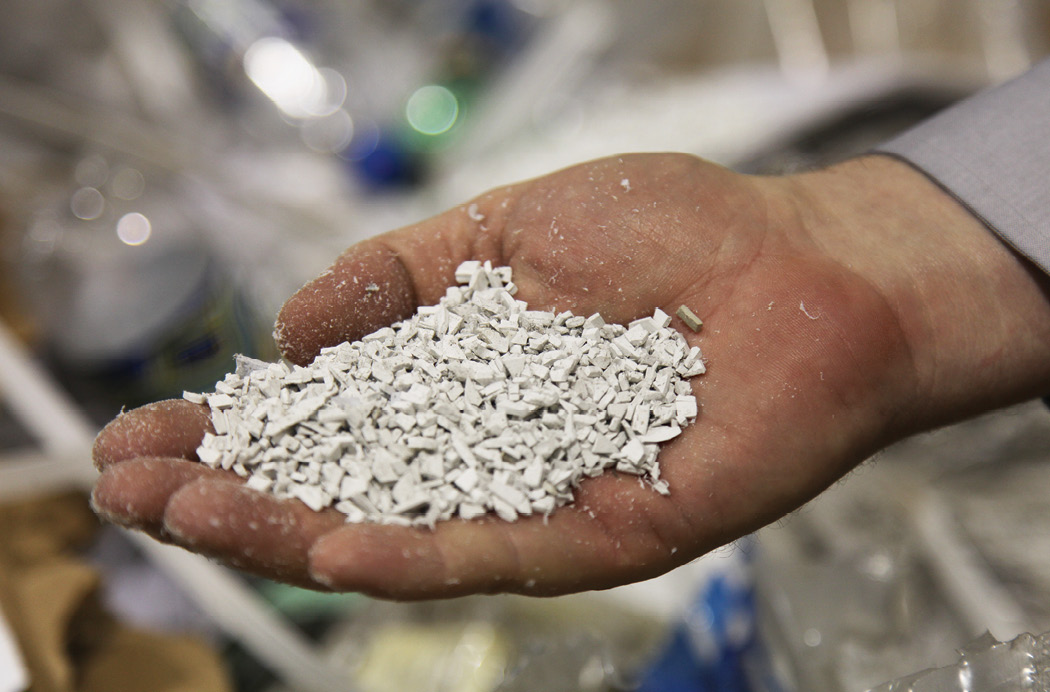
Above: Among its many environmentally friendly practices, VEKA employs sustainable practices in its manufacturing, including process water recycling and energy-saving technologies. VEKA also uses its customer’s cut-offs and plans an in-house recycling center for 2025.
Amid escalating requirements for building product manufacturers to be green, VEKA North America continues to rise to the challenge. The company embodies its commitment to a better future in its “We Care, We Act, We Grow” mission statement, which Window + Door and VEKA North America spoke about in 2023 at its headquarters in Fombell, Pennsylvania.
Window + Door visited VEKA in June to talk with Joe Peilert, president and CEO, and Kevin Seiling, vice president, engineering, about the company’s initiatives related to recycling, sustainable practices and the vinyl industry at large.
Window + Door: Why is environmental responsibility and recycling so important to VEKA?
Joe Peilert: We’re a family-owned business. When we created our mission statement, the owner family came up with this term called “enkelgerecht.” It’s a German term that means “worthy of the grandchildren.” Ultimately, we translated that into “future friendly.” The family is in its second generation of ownership now and has had a very strong commitment to sustainability and recycling.
WD: VEKA aims to be carbon neutral by 2045. Can you expound upon that goal and what it entails?
JP: Our overall goal as a global company is to be carbon neutral by 2045. We started measuring our carbon footprint in 2022 and tracking our improvement to make sure we achieve progress each year.
This goal also accounts for our supply base, so we capture things like transportation across all of the 24 plants VEKA has worldwide. Each production facility has a responsibility to report numbers back. We document our progress in our biannual Corporate Social Responsibility (CRS) report.
Our CSR focuses on four areas. One: long-term careers in a healthy and safe environment. Two: eco-friendly production wherein we employ environmentally responsible production processes, including process water recycling and extensive investments in energy-saving technologies. Three: design and supply thermally efficient, cost-effective vinyl profile systems for Energy Star 7 and beyond. Four: our commitment to recycling, which dates to 1993.
WD: Can you tell me more about the company’s recycling history?
JP: VEKA has pioneered recycling in Europe and has an infrastructure that goes beyond pre-consumer recycling to post-consumer recycling with its three plants in Germany, England and France. We’ve recycled over 25 million PVC windows since we started. In North America, there’s significant potential for growth in recycling. We need to work on regulatory hurdles, create cost-effective landfill alternatives and address logistical challenges, especially for longer distances.
WD: How are the North American locations recycling product and using recycled content?
JP: VEKA North America is dedicated to using 100% of our customer cut-offs, recycling internal start-up scrap and using additional sources of vinyl scrap for our Outdoor Living Products (OLP) business. To achieve that, we plan to establish an in-house recycling center by 2025 while simultaneously working with outside recycling specialists. As we explore post-consumer recycling options, I see additional opportunities for collaboration.
Not all scrap material can be readily reused in window profiles, such as colored material and profiles with weatherstrip. Separation and manual handling add cost to the process. Profile designs with recycled material often need thicker internal walls, which may add cost. We’re fortunate to have another outlet for recycled material with our OLP business. Growth in our fence business has allowed us to use additional sources of vinyl scrap, making us a net user of recycled material. We’re progressing and believe we can increase the recycled content over time.
There are also some secondary products we produce from recycled materials that are specifically in-house, including rack liners that go into window profile racks and prevent them from getting damaged.
WD: How does VEKA support sustainable practices beyond its products?
JP: We’ve made a lot of investments in the past couple years such as energy-saving lighting and using less power on extrusion lines. There is also the advocacy part of our business. Kevin is very engaged in FGIA and one of the leaders driving life cycle analysis (LCA) and environmental product declarations (EPD). That ultimately helps us as an industry and a company to properly portray the role vinyl windows can and are playing in providing cost-effective, thermally efficient solutions for homeowners. The LCA and EPDs provide proof there is not a more cost-efficient way to have an energy-efficient window today. That’s why you have north of 70% market share for vinyl windows in the residential space.
WD: Can you share more about the work with the LCA and EPDs?
Kevin Seiling: I’m the first vice president of the materials council for FGIA and wrote a grant application to fund a recycling study. There are several considerations in post-consumer recycling, including ensuring the windows are lead free, determining operator types and also the volume of windows being replaced. It turns out there’s a pretty substantial amount of material coming out of openings every year. There’s a big opportunity there for recycling.
At the same time, we’re working on an LCA. VEKA is one of six vinyl extruding companies that funded it; we hope to publish the LCA by September. The LCA is cradle-to-gate, meaning from the time we make it until we ship it.
Additionally, the EPD product category rules were updated this past year for windows, doors and skylights. So, we’ll take the updated PCRs, the new LCA and start making EPDs for vinyl windows. Our next step will be creating EPDs for our standard family of windows. We’ll also help our customers develop their own EPDs.
WD: What is the goal of the EPD? What will it ultimately do for the industry?
KS: The primary consumers of our products are architects and specifiers. If they’re working on a government building, for example, it’s generally owned and managed by the GSA, which engages in USGBC’s LEED program. LEED requires a certain number of points, which EPDs can contribute to. The window industry hasn’t caught up yet with other industries where EPDs are more commonplace. There are only a few that exist, so this will be the first real run at commercial products and applications where we can provide all the tools you need with the LCAs and EPDs to demonstrate the energy performance of these products. We want to offer our customers solutions that advance their environmental positioning as a competitive advantage.