Window-specific Issues in Modular Construction
While modular construction offers numerous benefits, window suppliers must carefully consider factors
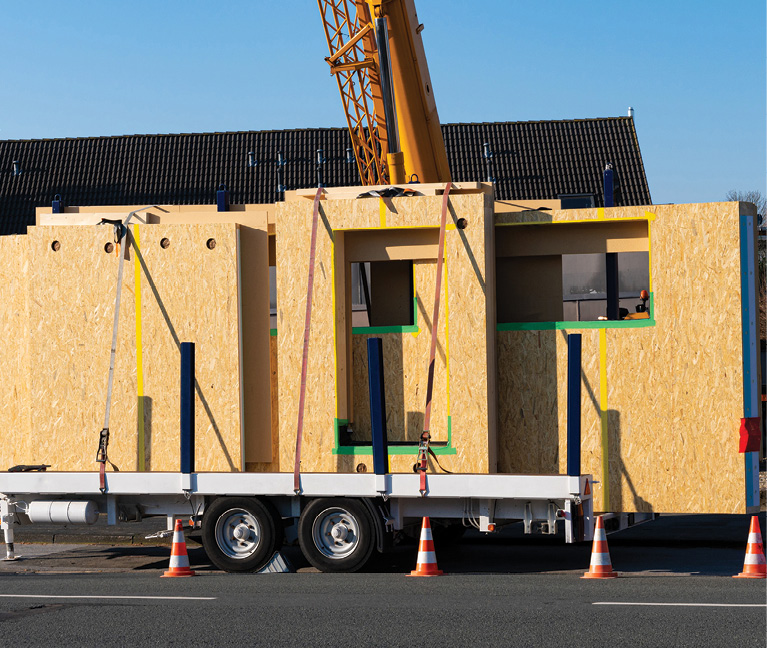
Modular construction is the practice of prefabricating large units and transporting them to another site where they are assembled to form a complete building. After the modules are transported and placed at their final destination, on-site construction crews complete additional work before occupancy.
Companies engaging in modular construction boast about the many benefits of off-site building: cost savings, reduced construction times, less waste and controlled building environments. For window companies, the benefits include having windows installed by people who routinely install the same product in a warehouse protected from the elements. Despite these benefits, there are a few concerns specific to windows that suppliers and manufacturers should consider when it comes to selling windows for use in modular construction.
Window selection
Selecting the proper window for the modular structure and its eventual geographic location is crucial to future performance. A window that works well in one geographic location might not be ideal for another based on weather conditions. When promoting a window for use in modular construction, consider the eventual location of the module rather than the market in which you are selling the window. Keep in mind that modular housing must comply with the International Building Code and any local regulations in the jurisdiction of the modules’ eventual location.
Careful consideration should also be given to the type or configuration of the window. The very concept of modular construction means the modules will be primarily built in one place and transported to another location for assembly and on-site finishes. Moving a module involves use of a crane to lift the module at its off-site location, placement on a truck, transportation to its final destination, lifting the module again and incorporating it into the larger structure.
Movement of and/or damage to the windows can occur if this is not done properly. Improper placement of modules on top of other modules on-site can also result in unwelcome structural stresses placed on windows in the lower modules.
Some of these risks may be avoided by determining the best frame material and window configuration for the application. Is vinyl better than aluminum to avoid compromising the miter joints? Is a simple standard-sized single window preferred over a multiple window configuration with mulls or other non-integral parts?
AAMA 502 testing
It is good to know at what point in the construction process AAMA 502 testing (if any) is to be performed. AAMA 502, Section 6.1 and Note 3, dictate that testing should occur “as soon as practical” after installation has begun so that if there are product issues they can be identified and remedied before a “substantial portion” of the project is completed. Testing windows prior to transportation allows it to occur early on in construction (within six months of installation) and at a time when any issues the testing identifies can be more easily remedied. It also ensures that only the window product as-installed is tested, rather than the window product as-installed plus the quality of transportation, placement and any undue stress loads caused by stacking modules.
The owner and/or builder likely want the windows tested after the structure is assembled on-site because they are interested in the performance of the windows in the fully assembled structure.
One way to please both parties is to test a window or two early on in construction and then test a couple more after transportation and placement on-site. This not only enables the parties to confirm early in the process that the windows installed off-site are performing properly, but also if there are failures during on-site testing it may be easier to trace them to causes unrelated to the manufacture of the window.
Documentation
Window suppliers and manufacturers can take additional measures to protect themselves against the unique risks associated with modular construction, such as including short statements or disclaimers in the terms of sale and warranty documents addressing windows in modular construction. These measures are especially important where the window company is unaware that its windows are intended for modular construction and where there is no input into when AAMA 502 testing will occur.