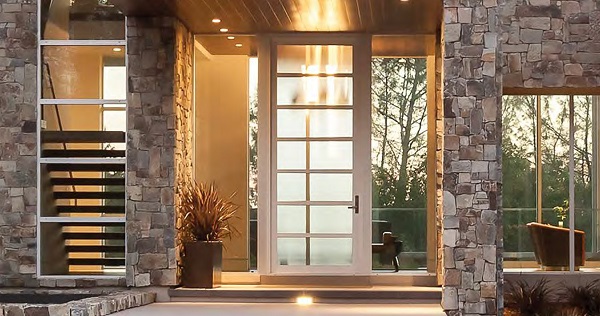
Prescriptive building codes are constantly evolving, forcing manufacturers to engineer increasingly thermal-efficient, aluminum doors. This is not as straightforward a task as it would seem. Hinge doors and sliding doors each present design challenges.
Hinge Doors
The main concern with hinge doors is the hinge placement in relation to the thermal break. The best-performing thermal breaks are made of polyamide (nylon) due to the material’s good insulating properties and excellent mechanical performance. This material also allows for wider profile options than other materials and methods. A wider profile means a larger separation between the aluminum extrusions to reduce thermal conductivity.
Centering the polyamide thermal break between the door’s interior and exterior aluminum extrusions offers the best thermal performance because it maximizes the space between the two extrusions. However, this placement creates a situation where the hinge screws into the thermal break. Over time, thermal cycling occurs and even polyamide can’t support the door’s weight. The screws loosen their way out, causing the door to fail.
There are two ways to engineer around this:
- Reduce the thermal break’s size and move it to one side of the door to avoid the hinge screws. A smaller thermal break, however, means a less thermally efficient door.
- Add an aluminum leg behind the thermal break allowing for the screws to be secured into metal. This will give the door more strength, but adding more metal creates a short-circuit, which decreases its thermal efficiency.
Either are imperfect options and will negatively affect the thermal performance.
Multislide Doors
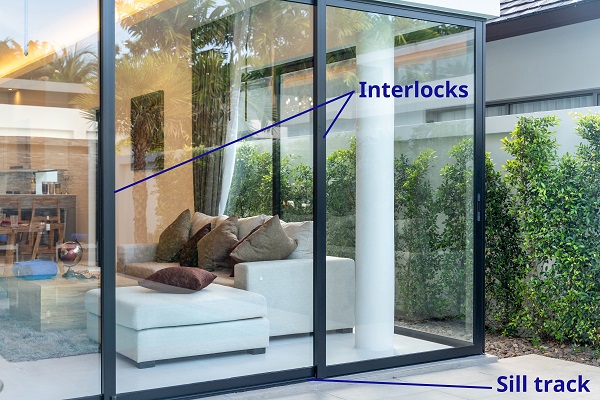
Multislide doors offer two main concerns: the interlock and the sill track.
The interlock is where the sliding door panels meet when fully closed. You’ll find the greatest amount of metal here because it is the door’s weakest part; reinforcing it makes it stronger. Unfortunately, because of the increased metal and how the interlock joins, air can travel more easily through it.
Engineering an air-tight, thermally broken interlock is very difficult. Even with a thermal break, if the metal pieces are too close to each other, the air path through the interlock can jump from one metal piece to another. There needs to be true exterior and interior separation to completely thermally break an interlock. Applying the thermal break in a 90-degree configuration accomplishes this.
The sill track also poses challenges because it goes across the door’s entire opening. When the door is closed, sill sections running from interior to exterior can create an energy short-circuit. The only way to combat this is to completely thermally break the sill, from front to back, at each location where a closed panel would rest. It’s not the most aesthetically pleasing solution, and can create fabrication and installation issues.
We must apply the insights gathered from thermal simulations, consultants, design experts and energy advisors to develop the best possible solution. Drawing from all available information and innovation, you can engineer the optimal, holistic, high-performing hinge or multislide door.