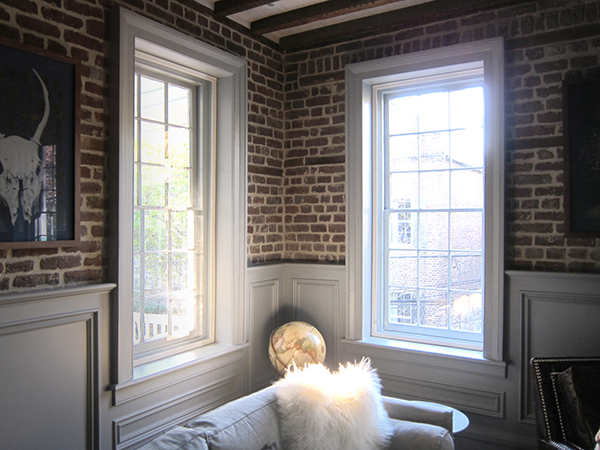
Indow founder and CEO Sam Pardue's classic 1906 Portland Craftsman house had a historical structure and original architectural features; however, its single-pane glass windows were leaky, boosting his gas bill and wasting a significant amount of energy.
“Windows are in very harsh environments and undergo a wide range of temperatures through the day and year,” says Pardue. “With the sun beating down on a summer afternoon or a freezing wind blowing on a cold winter night, the cavity can get up to 130 degrees Fahrenheit or more, or down to -40 degrees Fahrenheit or less, which causes the acrylic to expand and contract. We needed compression tubing that not only consistently stayed tight but did so even as the edges of the window thermally expanded and contracted.”
Pardue realized to find an optimal solution, choosing the right material was crucial. After researching multiple materials, Pardue concluded that silicone was the best material because of its compression set and temperature resiliency.
Cooper Standard ISG
“With research, we found that there are quite a few silicone extruders out there, but Cooper Standard ISG rose quickly to the top of our list,” says Pardue. “It’s rare to find expert engineers who specialize in designing silicone seals from scratch.”
He also found that Cooper Standard ISG was one of the few companies who formulated their own silicone as opposed to buying it from third parties.
“Their vertical integration and deep knowledge of the material properties allowed them to create a custom silicone recipe for us that optimizes both performance and aesthetics,” Pardue says. “They were not only able to build in compression strength and other performance properties we needed, but they also assisted with assembly and operation, and served as a host of aesthetic properties.”
Cooper Standard ISG helped create the Indow inserts, which gained enough popularity to be featured in several episodes of the television show “This Old House.”
“The inserts leave your existing windows almost completely untouched, thanks to the patented compression seals that press into place and stay tight for the long term,” says Pardue. “The inserts are basically invisible once they are installed, and yet, the U.S. Department of Energy found they can lead to a 20% reduction in heating and cooling costs.”
A valuable partnership
Pardue notes that the initial selection of Cooper Standard ISG as a supplier has led to a 12-year partnership that is continuously growing, along with a constant stream of value-added efforts to benefit both companies.
“Cooper Standard ISG helped us develop the initial silicone material and extrusion dye that we used to start the company and we’ve been working with them ever since,” he says. “In fact, in 12 years we’ve never had a durability-related warranty issue relating to the silicone compression bulb—that speaks to the high quality of their formulations and manufacturing.”
Cooper Standard ISG has also made efforts to continually add value to the partnership. During its partnership with Pardue, these efforts have included continued new product development, such as the creation of seals for Indow kits, a line extension which allows homeowners to benefit from a new type of seal that expertly combines silicone with ABS plastic for ease of installation.
“Innovation can best happen when you have a partner that helps you bring your idea to fruition,” says Pardue. “There is no doubt in my mind that Cooper Standard ISG has been an indispensable part of the Indow growth and success story. Without their expertise, we would not be where we are today.”