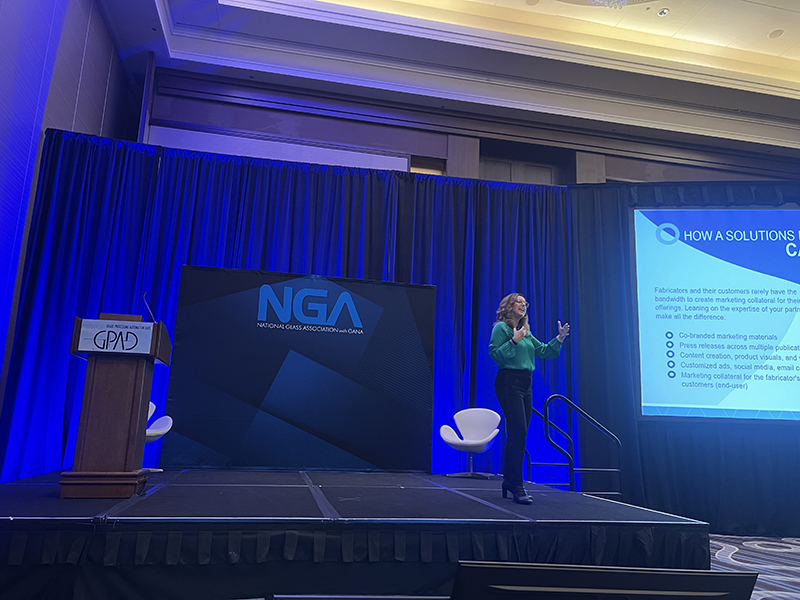
Glass Processing Automation Days was held in Nashville, March 5-6, 2024. Automation took center stage at this year’s event, but also featured talks on AI, product launches, glass distortion, tempering, lamination and fabrication.
Implementing automation
According to Nicola Lattuada of Lattuada North America, there are four steps fabricators should approach projects with involving automation and robotics.
- Step 1: Select the process to be automated. Ask yourself, what causes headaches for people most frequently? Which processes take the longest to complete?
- Step 2: Think about the people. Change doesn’t happen overnight. How will your team react? Automation can change existing roles and processes, which leads to concerns. Train your workers.
- Step 3: Define objectives and scope. Set goals.
- Step 4: Technology selection process. Compare different proposals. Lattuada says this is one of the most critical steps, since it’s the most difficult to change after the fact.
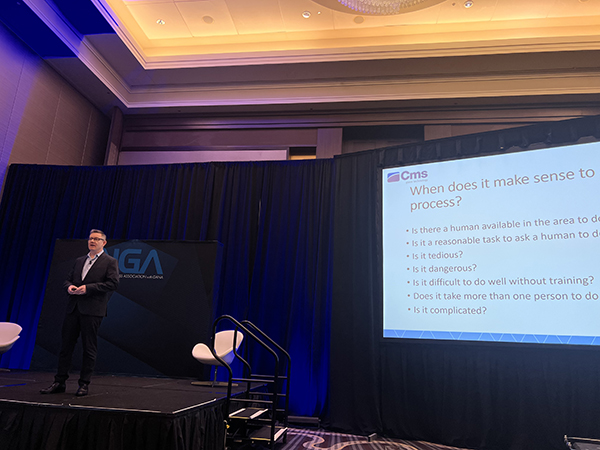
The benefits of automation, internally, should include increased efficiency, productivity, improved accuracy, consistency and a competitive advantage for the company. Externally, benefits should include improved client response, more value to clients faster, improved company image, innovation, energy efficiency and optimization.
Johnathan Paredes of Bovone says second level glass processing companies are taking their production to the next level by enhancing automation, maximizing production, raising flexibility and maximizing safety standards. Robotic systems allow for a more linear throughput for the edging system, meaning shorter lead times; increasing the quality of the product.
When it comes to “avoiding the automation scaries,” Chris Cullum of CMS Industries says “you have to walk before you can run.” When incorporating automation into your workplace, Cullum says it often makes sense to do so when adding a new expansion, rather than integrate into an existing process.
Plant layout is also important to keep in mind. How will things go through your plant? You don’t want physical bottlenecks where you can’t move things because it’s too tight. You also need to build a solid foundation; partner with a good software company, hire a dedicated programmer, someone with CAD and CAM knowledge and experience.
Click here to read about AI at GPAD.
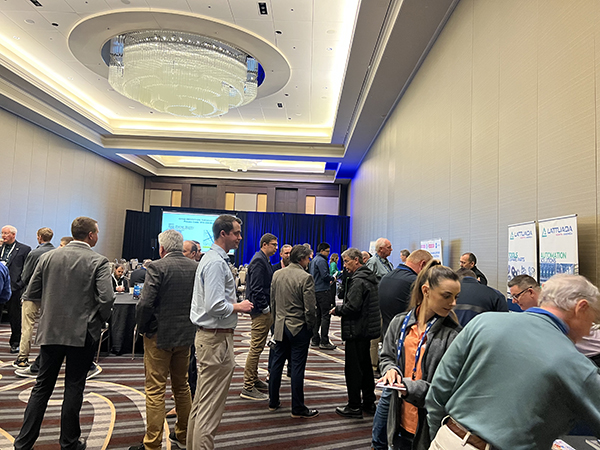
Keys to product launches
Syndi Sim of Diamon-Fusion International led an engaging discussion on how to successfully launch a product or product line. You always want to have goals set up, like to capture new customers, upsell existing customers, differentiate your business, new/increased revenue stream, or create more value for the fabricator, she says. Sim says it is vital that you also have a strategic partner.
The product pre-launch is the “bulk of the work.” This is the most important step. This phase includes market research, identifying the target audience, creating the launch plan, train and educate sales team, develop market collateral and develop clear communication across all teams.
“Your sales teams are critical in the success of a launch. They are the key to our success,” says Sim.
Your solutions partner should educate the fabricator sales team on regional footprint, competing products, train on key value propositions and product differentiators, product demonstrations and review common customer questions. Your partner should also be creating press releases, social content and create marketing collateral.
For the launch itself, “Communication to the industry is critical. How do your customers receive news and updates? You want to make sure you’ve done everything. It’s your day to scream it from the mountains,” says Sim.
Post-launch, allow adequate time. Review the status of the new product about 6 months afterwards. Get insight from the sales teams and customers. Once you get that feedback, you have to implement it. After that, continue to keep the launch momentum going.
Glass and quality assurance
Ric Schmidt of Viprotron says there are many benefits to accurate measurement of glass tempering distortion. If your glass is distorted, it could likely be an issue with the furnace.
The recently launched Temper Scanner 5D, with the all-new Rollerwave and Edge Kink channel, is easy to retrofit and includes a white haze scanner and anisotropy scanner. These can detect what is necessary to improve furnace parameters. All of this housed in a concise rack with no modification required on your line. Integration is right at the exit of the furnace.
Nate Huffman and Eric Hegstrom, LiteSentry-SoftSolution-Strainoptics also discussed glass distortion, specifically how Optical Power in millidiopters is a better representation of distortion than typical peak-to-valley measurements.
High quality is important in tempered glass, says Mike Synon of HHH Equipment Resources, including strength and durability, resistance to thermal stress, reliability and consistency, safety standards compliance and long-term performance.
Common tempering issues include meeting ANSI Z97 specifications, quality edgework and aesthetics. Root causes of these issues include temperature, uneven cooling, equipment malfunctions, roller wave and bow/warp. Best practices to follow are to ensure your heaters are in working order and periodic maintenance.
Synon says when it comes to monitoring and continuous maintenance, “assign someone on your team to do this on a daily basis.”