Aluminum Extrusions
Aluminum can meet many goals, including those around sustainability, recyclability and design
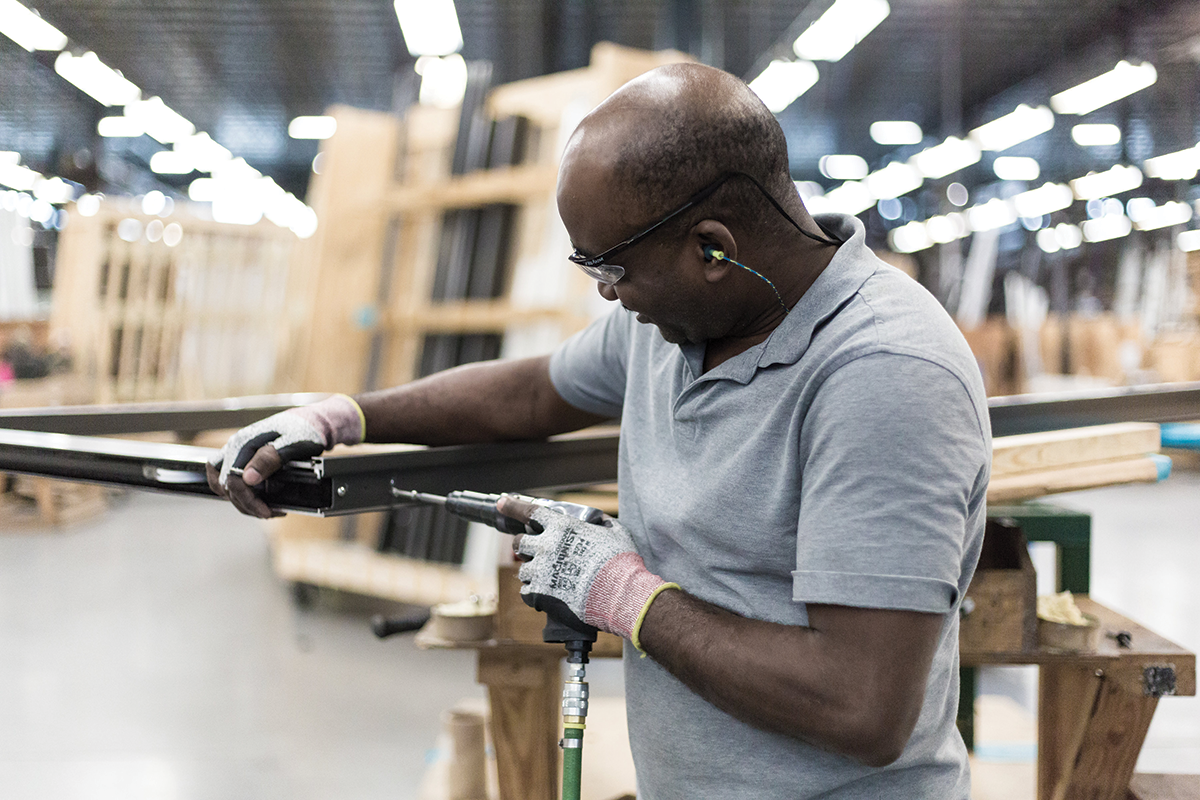
Above: An employee works on a product of aluminum extrusion, Courtesy of PGT Innovations
Aluminum extrusions are aluminum products, which can include window and door components such as frames and panels as well as automobile parts and other uses, manufactured by pushing the aluminum through a die to create the desired shape or form.
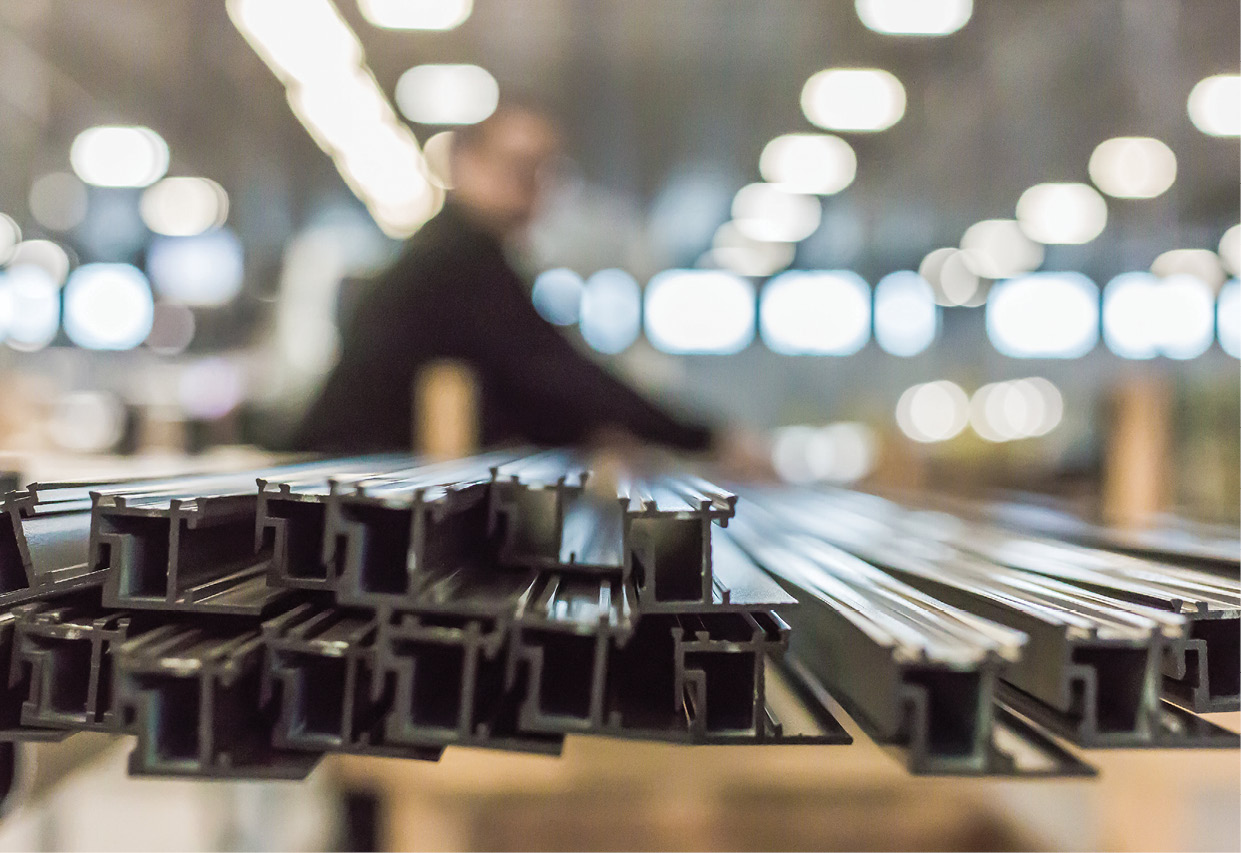
How are they made?
Before this can happen, however, aluminum in the shape of a log is heated to around 900 degrees Fahrenheit to make it malleable. After being cut into smaller pieces called billets, it is then forced through the die using a hydraulic ram that uses about 3,600 tons of pressure. Afterward, the aluminum extrusion cools to room temperature on a cooling table or rack.
Keymark Corp., a U.S.-based, full-service, aluminum extrusion company, has its own homogenizing oven at its Fonda, New York, facility where aluminum logs go through a homogenization process to get rid of any impurities. This extra step aims to provide customers with what the company dubs a “premium quality product” for their aluminum extrusions.
According to Brent Slaton, national sales coordinator, Keymark, the oven aims to eliminate residual stress produced during casting and improves metallurgical results. After being homogenized, internal elements of aluminum billet are consistent. The homogenizing process features less mold consumption and improved surface quality of the billet. It goes through the homogenizing oven after casting and before the extrusion process. Slaton says it is a crucial unit for enhancing the quality of aluminum profiles.
“In a way, aluminum extrusions are similar to Play-Doh presses. You put Play-Doh in it, squeeze the lever down, and you get a star, or a square, or a bar. It’s the same exact thing, just on a grander scale using aluminum,” says Scott Condreay, architectural engineering manager, Hydro Extrusion North America, a global company that specializes in custom aluminum extrusions.
Indicators for aluminum extrusions
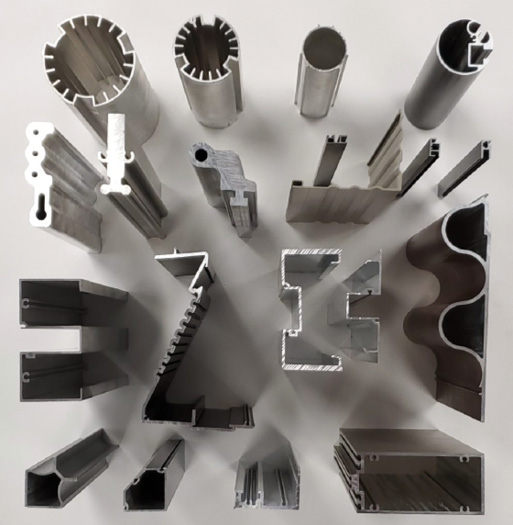
Sustainability is a huge draw for aluminum extrusions. Unlike vinyl and steel, which can be recycled one or two times, aluminum is infinitely recyclable. According to The Aluminum Association, nearly 75 percent of all aluminum ever produced is still in use today. In most industrial markets, like automotive and building, recycling rates for aluminum exceed 90 percent. Recycled aluminum saves 95 percent of the energy needed to make new aluminum.
Condreay says Hydro purchases post-consumer scrap for its aluminum extrusions, so the company is making a less significant impact on the environment. Aluminum hardly makes its way to landfills, with the ability to continuously resell scraps.

“Aluminum is lightweight, it’s corrosion resistant, it’s very resilient. The strength-to-weight ratio is great. It’s non-combustible and non-toxic compared to other materials,” says Slaton.
“One of the other biggest benefits of aluminum extrusions is the array of colors you can achieve. The spectrum is endless; you can get any color under the rainbow whereas some of the other competing materials are limited as to pigments and colors they can achieve. With aluminum, you can anodize it, paint it—both wet and powder—and you can achieve high gloss and low gloss,” continues Slaton.
Aluminum has a higher yield strength and typically a longer product life. The cradle-to-cradle sustainability factor of aluminum is infinite when recycled without degradation of properties, according to Slaton.
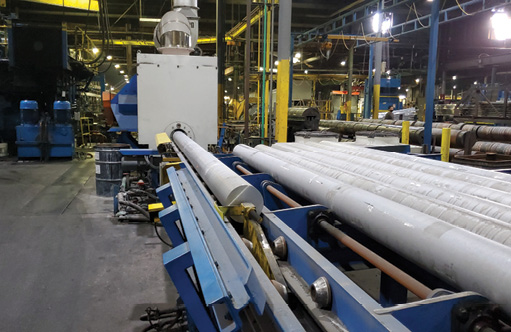
One of aluminum extrusions’ limitations is its high conductivity. Aluminum allows for greater amounts of heat loss in buildings because it is more difficult to weld and fuse corners, whereas it’s easier to do so with vinyl.
However, Dean Ruark, vice president of engineering, PGT Innovations, says that new technology is helping solve that issue. Special thermal breaks can now allow aluminum to be used in buildings in colder climates. After attending the most recent International Builders’ Show in Las Vegas in early February, Ruark says he’s seeing a resurgence of aluminum within the industry because of this. With these new gadgets, aluminum is beginning to meet energy codes in colder climates.
PGT Innovations manufactures aluminum impact-resistant windows and doors. To make these, the aluminum must first be extruded to make everything from the sill to the frame, sash, panel, and even more components. PGTI works with an aluminum extrusion company to create dies specific to its products.
“Aluminum is also great for narrow sightlines. There’s a huge trend right now of all glass and unobstructed views, aluminum is great for that because of its ability to be extruded into many shapes. It’s really limitless what an architect can do with that product,” says Ruark.
Aluminum Products
View these aluminum products from LaCantina, Weather Shield, Marvin, Akotherm and All Weather.