Gas Fill 101: Gas fill options for IGUs
Plus three methods to test gas in a unit
When an insulating glass unit is “gas filled,” it has had the air in the cavity replaced with a fill gas and sealed. Typically, the fill gases used in an IGU are argon, krypton and xenon. All three gases are less conductive than air and are designed to increase the center-of-glass performance by reducing the U-factor. The goal in using any of the three fill gases is to lower the thermal conductivity and lessen heat conduction through the cavity.
Krypton and xenon will yield roughly the same performance as argon but in two-thirds to one-half the cavity width. Using krypton gas will allow an overall thinner unit and is often used with triple-pane construction. The chart shows the varying U-factors with glass spacing and argon and krypton fills.
Below: Center-of-Glass U-factor (IP) vs. Glass Spacing Double Glazed Low-E 0.04 Argon and Krpton Fills
Gas percentages represent initial fill rates achieved, balance assumed to be air. Calculations performed using Window 5.2 computer program by WESTLab.
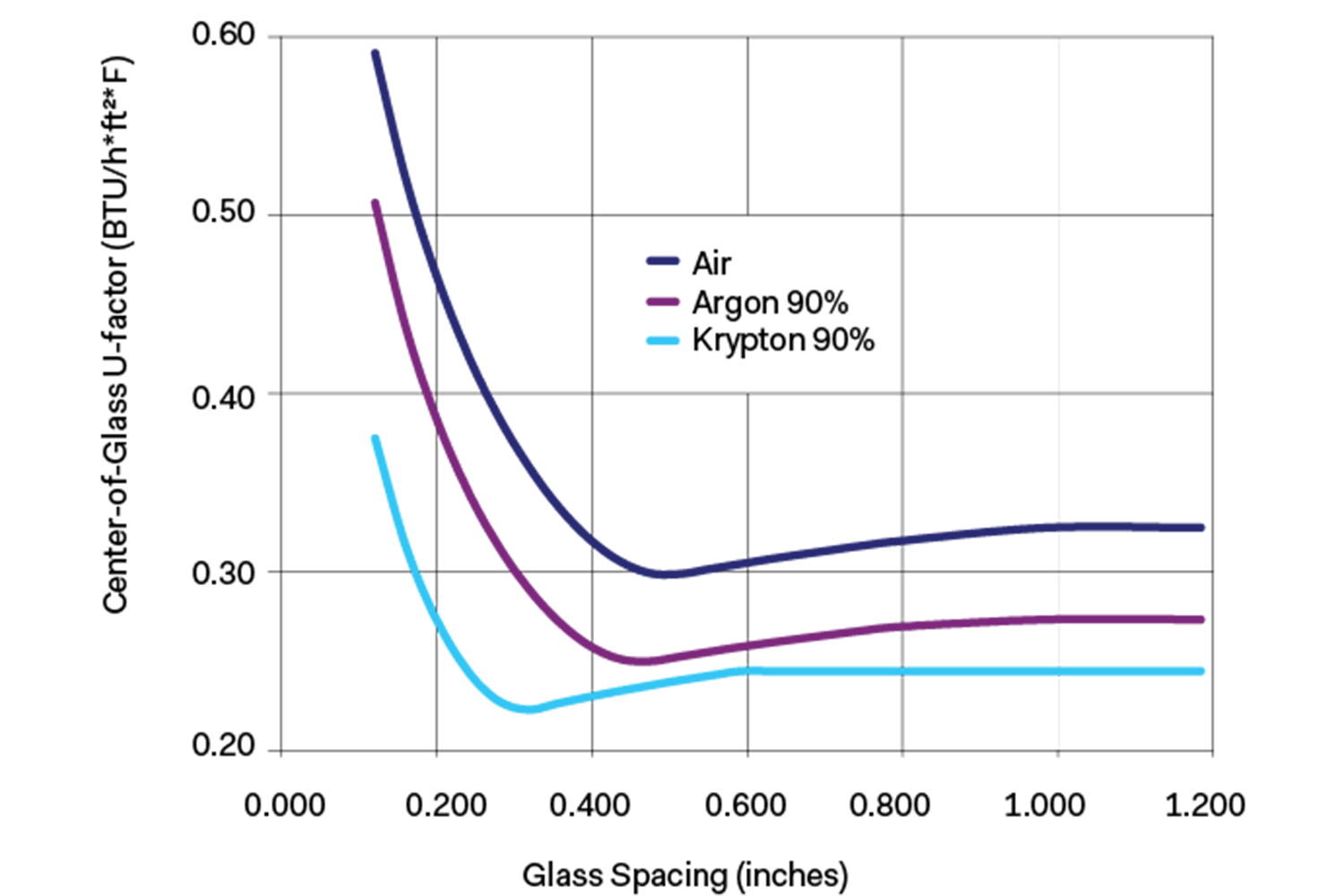
Concerning leaks
Does the gas in a sealed IGU really leak out? Yes, but it’s a two-way street. For the gas concentration to become lower inside the airspace, another gas needs to dilute it. For example, if there is a balloon filled with helium and some of the helium is let out, the balloon will still be 100 percent full of helium—the balloon size has decreased but the volume concentration is still 100 percent. To say that the balloon contains 90 percent helium, some other gas needs to dilute it (such as a puff of air).
Take this example back to IGUs. The IG industry has conservatively said that argon will “leak” at a rate of 1 percent per year, but remember that two-way street. Argon is going out and air and water vapor is coming in. If, hypothetically, a sealed unit experienced an influx of air, the percentage of argon concentration would decrease without any argon actually leaving the unit.
NGA Glass Technical Paper
The Technical Services Division of the National Glass Association produced a Glass Technical Paper, Performance Improvements in Insulating Glass. The center-of-glass thermal performance of an IGU is a function of glass type, coating, and size and gas fill of cavity gap. This document addresses those areas and does not address IGU edge conditions.
A number of factors weigh into how fast the gases travel directly through the sealant or across the bond line (sealant and glass, and sealant and spacer interfaces). Manufacturing defects—such as sealant voids and contamination, as well as permeability through the primary sealant—are the modes of transport. The driving forces are partial pressure difference of the gases (cavity space vs. atmosphere), temperature changes, barometric pressure changes and wind loads.
Now that we know the gas can leak out and air and water vapor can leak in, how can we test how much fill gas is still in the unit? There are three methods for testing the gas content in an IGU that has already been sealed.
Three test methods
1. Destructive testing
Destructive testing involves breaching the seal to extract a gas sample with a syringe that can be injected into a gas chromatograph (GC) or oxygen gas analyzer. The GC has historically been the “gold standard” for cavity gas measurement because it is very accurate and can measure multiple gases at once (oxygen, nitrogen, and argon or krypton). There are different types of detectors that can be installed on the GC but the most common is the thermal conductivity detector (TCD) for measuring these gases. Besides being the gold standard, it is also probably one of the most finicky pieces of equipment to operate listed in this article and requires a well-trained operator.
The head space oxygen analyzer is used in a similar fashion to the GC, where a syringe extracts a gas sample and is injected into the analyzer. The difference is that only the oxygen is analyzed, so any other gases such as nitrogen, argon or krypton need to be extrapolated (see section titled Extrapolation When Measuring Oxygen Only).
2. Non-destructive testing
Non-destructive testing is accomplished with the use of a spark emission spectroscopy (SES) or tunable diode laser absorption spectroscopy (TDLAS).
The SES method utilizes a spectrometer to monitor a high-voltage spark that is created through the glass to the inside of the cavity. The spark creates a release of photons that the spectrometer analyzes for certain frequencies of light in the UV and visible spectrum; the resulting argon or krypton content is reported. Because oxygen is one of the gases measured by an SES, when measuring IGUs that have been aged, there is some concern of error if the ratio of oxygen and nitrogen is different than that of the air we breathe. Thus, it is partially affected by the extrapolation section (see section titled Extrapolation When Measuring Oxygen Only).
TDLAS measures by means of a laser tuned to the absorption line of oxygen. A detector senses the signal intensity and relates it to the amount of oxygen in the IGU cavity. The oxygen content is then mathematically converted to display argon or krypton content.
TDLAS is limited by measuring oxygen only and is subject to the extrapolation section.
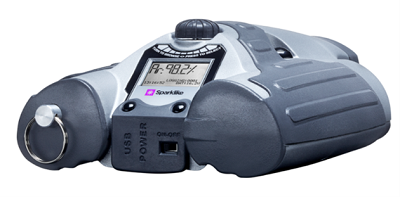
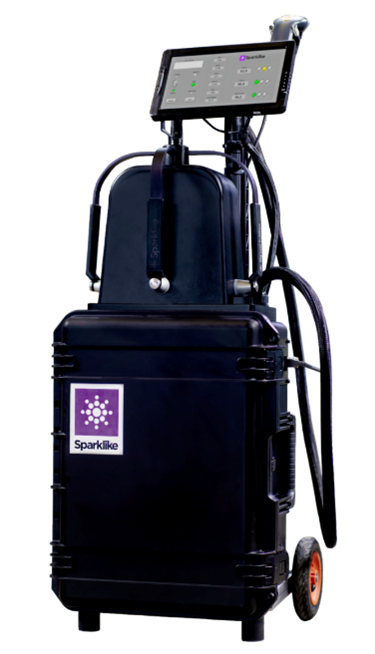
Extrapolation When Measuring Oxygen Only
The extrapolation method requires a bit of guesswork, decreasing the final accuracy. For example, if a sealed unit contains 90 percent argon and 10 percent air, we know the oxygen content should be 2.08 percent if measured with an oxygen analyzer (10 percent air is made up of roughly 7.8 percent nitrogen and 2.08 percent oxygen). Once the oxygen is known, the resulting gas can be calculated using the equation 100-(100/20.8*O2).
The major limitation with measuring oxygen is that we expect its ratio with nitrogen to be the same as the air we breathe. Since we know there can be differential permeability and possible off-gassing from desiccant, we can’t rely on the ratio to be unchanged. This is what decreases accuracy.
Taking that same example of a 90 percent argon-filled unit, if nitrogen is decreased to 7.7 percent and oxygen is increased to 2.18 percent, an oxygen analyzer would extrapolate the argon content to 89.5 percent even though we know the argon is 90 percent. Much larger variations have been seen in real life examples and verified using a GC.
3. In-situ gas testing
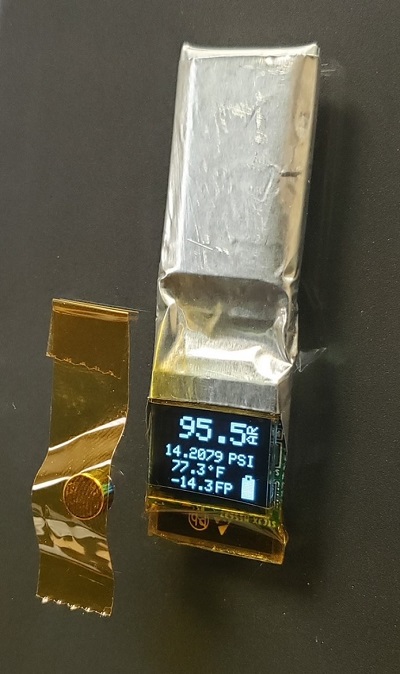
In-situ gas testing is accomplished by installing a sensor inside the cavity at the time of manufacture. One type of in-situ sensor is a sticker-type product that is placed inside the cavity; an external wand measures the optical fluorescence decay of a dye on the internal sticker to determine the amount of oxygen in the IGU cavity. The OpTech sensor is limited by the extrapolation section.
Another in-situ gas sensor measures the total thermal conductivity of the cavity gas. The inside the insulating glass (iTiG) sensor measures gas using a thermal conductivity sensor similar to a GC. The iTiG comes in a small package and doesn’t require pulling a sample with a needle. Since it is powered by wireless inductive power transmission, there is no breach in the seal; the unit seal has full seal integrity. The sensor can be calibrated for argon or krypton and also measures temperature, absolute pressure, relative humidity, frost point and UV light.
The sensor measures the total thermal conductivity of the gas and uses that to determine the argon or krypton content. Therefore, it is not limited by the extrapolation method like many of the other measuring types are.
Measuring
Why it’s important, when to do it, what it tells you, how to troubleshoot
Measuring is done to make certain the customer gets what they think they are getting. Measuring may be conducted for the following reasons, among others:
- Certification: required for energy codes and for Energy Star
- Quality control: to make sure product going out the door meets specifications
- Production control: to make certain production equipment is working
- Receiving of product: many builders, architects are requiring incoming product be tested
- Insurance: units are being tested after weather events like hurricanes
- Building maintenance: units tested to predict ultimate replacement
- Research: units tested to see if building is performing as designed