Q+A with Joseph Machine Co. | Workforce Needs in the Age of Automation
How automation can help companies combat the labor shortage, enhance safety and maximize resources
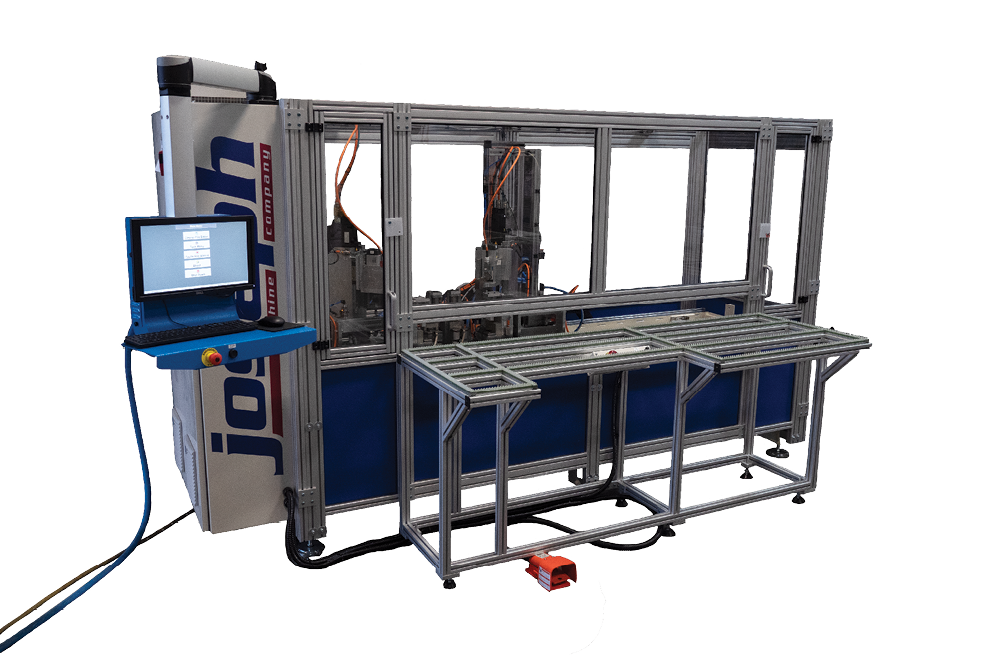
The skilled labor shortage has long been an obstacle for the industry. As the supply chain issues that dominated the past few years are easing, labor is again coming to the forefront of companies’ top challenges.
David Kline, vice president of sales and marketing, Joseph Machine Co., and CEO Anthony Pigliacampo talked with Window + Door about the current workforce and how automation can help companies alleviate their workforce challenges and enhance safety on the manufacturing floor.
Window + Door: Let’s start with an industry overview. What are some trends in the window and door manufacturing industry that Joseph Machine is keeping an eye on?
David Kline: The U.S. market continues to focus on higher efficiency designs using materials that are more difficult to fabricate, such as thermally broken aluminum and fiberglass extrusions. They are much more challenging to fabricate than PVC and are great places to apply automation. Another important trend is the continued focus on finding ways to make workers’ jobs easier. The ergonomics of using equipment are more important than ever to enable workers of all shapes and sizes to be equally productive.
WD: How has the workforce changed in the past five years? How do you anticipate it will change moving forward?
Anthony Pigliacampo: The workforce is experiencing a significant shift due to the retirement of baby boomers and the impact of the COVID-19 pandemic. As a result, many workers have left the industry, leaving a shortage of skilled workers. To combat this, companies must attract and retain younger workers with different skills and work preferences. Companies will be forced to automate to have acceptable working conditions and produce more with less. These trends are likely to remain the same.
WD: Recruitment and retention are huge challenges. How are you targeting younger workers for a career in manufacturing?
DK: This is a challenging problem in the U.S. College prep is seen as the ‘only’ path to success when, in reality, manufacturing can be both stimulating and financially rewarding. We spend a lot of time connecting with local and regional schools to help our company gain exposure, conducting tours for student groups, and hosting interns from local universities.
WD: What key skills must today’s labor force have?
AP: Today's labor force needs to have a mix of technical and soft skills. Technical skills include proficiency in automation and digital technologies, such as computer-aided design (CAD) and programmable logic controllers (PLCs). Soft skills include communication, collaboration, problem-solving and adaptability. More automated equipment in plants means more digital fluency for workers is necessary. Troubleshooting machines is often handled on a screen now instead of with a toolbox.
WD: Automation can be a great solution for labor needs. Another area that can benefit manufacturing facilities is safety. How have safety requirements and awareness evolved?
DK: The biggest changes we see are industry-wide adoptions of standards to prevent injury, such as light curtains and cabinet interlocks to prevent access to areas where cutters are still moving. These systems make equipment more complex; the software has also had to evolve to make troubleshooting easier.
The equipment is much better at telling operators what sensors have tripped and how to reset them. We see customers focusing on safety across their entire factory, not just the complex fab centers. For example, we have seen a mass migration from chop saws to enclosed upcut saws. This change is driven purely by a desire for a safer environment.
WD: What are the safety benefits of machinery?
AP: The systems required to make a machine ‘safe’ often enable more data collection and can help operators understand if a machine is operating properly or not. Maintenance-induced errors can decrease because the machine can tell the operator exactly what sensor is tripped. Machines with added safety are often much less prone to operator-induced problems as well.
WD: How has Joseph Machine positioned itself as a go-to machinery supplier for the industry?
DK: Customer service and support is our number one focus. Our machines only make our customers money when they are functioning. We believe our service sets us apart. Further, as an engineering-focused company, innovation is in our DNA. We are always trying to develop solutions to make our customers’ businesses easier to run and more profitable. Our Lock and Keeper insertion machine is a great example. It’s a small piece of equipment, but it helps make a repetitive, injury-prone job easier. Customers love that we help them solve those types of problems.
WD: How do you continually support customers, from those just getting started with automation in their facilities to those with fully integrated automation in their processes?
AP: Support comes down to resources. We have a large team of dedicated service technicians and personnel who are obsessed with solving our customers’ problems. We also have a 15,000-square-foot stock room of parts ready to send to a customer in need. Our large team of engineers are also incredibly helpful at solving complex customer service problems.
WD: How does Joseph Machine differentiate itself from its window and door manufacturing industry competitors?
DK: Being an American OEM allows us to offer service that is just not possible for companies based in Europe or Asia. We can support our customers in real-time. Our background as a custom equipment manufacturer also means we can better address our customers’ specific needs. We can understand the requirements and develop a solution perfectly matched to the need.